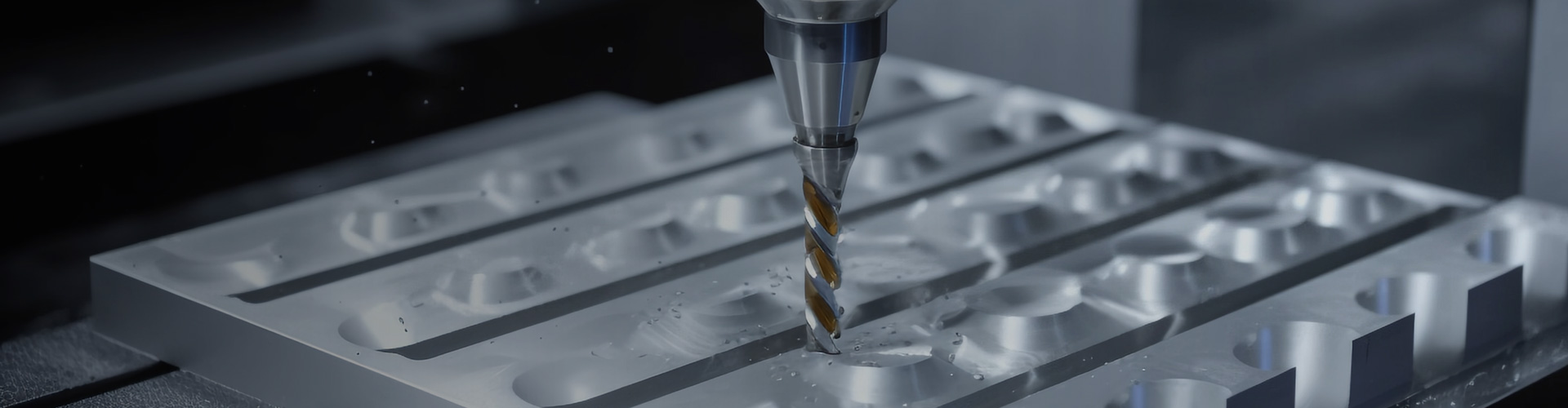
Type of Rivets: The Unsung Heroes of Assembly
Fasteners are essential in almost every industry, holding materials together to form sturdy and reliable assemblies. Unlike screws or bolts that rely on threads for detachable connections, rivets create permanent joints by deforming the tail. This ensures a strong connection even under significant stress and vibration. But what makes rivets special? How can they join diverse materials like metals, plastics, and wood, especially when only one side of the joint is accessible?
You'll find the answers here. This article delves into rivets, covering their advantages, disadvantages, types, and uses. Let's start with what a rivet is and how it works.
What Is a Rivet and How Does It Work?
A rivet is a mechanical fastener for creating permanent joints. It usually has a head, a shank, and a tail. Some, like blind rivets, also have a mandrel. Rivets are commonly made from aluminum or steel, but materials like copper are also used.
To install a rivet, it's inserted into a slightly oversized pre-drilled or self-pierced hole, with the head on the accessible side. Then, tools like a hammer, rivet gun, or hydraulic press deform the tail. This forms a second head (shop head or bucktail) on the other side. As the tail deforms and expands, it clamps the materials tightly, creating a robust, permanent connection. In the case of blind rivets, a stem is pulled through to expand and secure the joint.
Advantages of Rivets
Rivets are a versatile and reliable fastening solution, offering several key benefits:
High Strength: Rivets create durable, permanent connections that can withstand significant stress and vibration, especially under shear or dynamic loads. Unlike screws or bolts, they're less likely to loosen over time due to vibration or fatigue, providing long-lasting, secure joints in high-stress environments.
Rapid Installation: Many rivets are designed for quick and easy installation. For instance, blind rivets can be installed in seconds using a pneumatic or handheld rivet gun. Some types, such as blind, drive, and self-piercing rivets, only require access to one side of the joint, unlike other joining methods.
Low Cost: Rivets are generally cheaper than bolted connections and don't suffer from thread wear. They're a cost-effective alternative to bolts, especially for permanent connections. Their simple design and installation also reduce labor and material costs.
Disadvantages of Rivets
No solution is without limitations, and rivets are no exception. While they have many benefits, they also have some drawbacks:
Limited Flexibility: Unlike bolts or screws, rivets can't be adjusted after installation. Once in place, they're hard to remove or reuse. Removing them requires drilling, which is time-consuming and may damage surrounding material. They're also less suitable for thick materials or high-strength applications where bolts are often a better choice.
Potential to Weaken Material: Installing rivets involves drilling holes, which can weaken the surrounding area, especially in brittle materials or those prone to cracking.
Not Leak-Proof: Most rivets, like standard and blind rivets, don't provide a seamless seal like welding. Additional sealing materials or treatments are usually needed for waterproofing.
Increased Joint Weight: Rivet joints are typically heavier than welded or brazed joints due to lap joints or cover plates. This can be a problem in weight-sensitive applications.
Types of Rivets
Now that we have a general understanding of rivets, let's look at the different types. Each type is designed for specific applications. Here are the seven most commonly used rivets in product design and assembly:
Solid Rivets: Solid rivets are the oldest type, with a basic construction of a head and cylindrical shank. The head can be various shapes. They're installed by deforming the tail with a hammer or rivet gun. Sometimes, they're heated to make deformation easier. Solid rivets are strong and used in heavy-duty applications like airplanes, bridges, and ships, as well as in structural steel frameworks and historical armor restoration.
Tubular Rivets: Tubular rivets are like solid rivets but have a hollow shank on one side, requiring less force to deform. There are full tubular and semi-tubular types. Full tubular rivets are lighter and used in lightweight and decorative applications. Semi-tubular rivets are stronger and used in medium-strength and quick-assembly applications.
Split Rivets: Split rivets have two parts: a body with a head and a split tail. After insertion, the legs are bent to secure the joint. They're light-duty and suitable for plastics, textiles, and thin metal sheets.
Blind Rivets: Also known as POP rivets, blind rivets can be installed from one side. They have a mandrel. During installation, the mandrel is pulled, expanding the tail and forming a second head. When the right clamping force is reached, the stem snaps off, making a "pop" sound. They're practical and cost-effective for lightweight applications with limited space.
Drive Rivets: Similar to blind rivets, drive rivets can be installed from one side but don't need a mandrel. They're driven by striking, expanding the tail. They're easy to install without specialized tools, making them popular for quick-assembly tasks, but they're not suitable for high-strength connections.
Self-Piercing Rivets: Self-piercing rivets don't need pre-drilled holes and don't pass through the second material completely. They pierce the top layer and deform in the bottom layer. They create sealed joints, ideal for applications with high sealing requirements, and can join dissimilar materials.
Flush Rivets: Flush rivets, or countersunk rivets, have strength similar to solid rivets. Their conical head sits flush with the surface, reducing air resistance and improving aesthetics. They're used in aerospace and high-performance automotive industries but require more precision to install.
Materials Used for Making Rivets
Rivets are made from various materials to meet different application needs, considering factors like strength, durability, corrosion resistance, and weight. The choice depends on the rivet type and operating conditions. Here are the most common materials:
Aluminum: Aluminum is widely used for rivets because it's lightweight, corrosion-resistant, and ductile. Aluminum rivets are easy to install, like blind rivets that can be set with a hand tool.
Stainless Steel: Stainless steel rivets have excellent corrosion resistance, suitable for marine, chemical, and outdoor applications. They're harder to deform but have high tensile strength for high-stress environments.
Low Carbon Steel: Low carbon steel, or mild steel, is popular due to its affordability, strength, and workability. It's softer than high-carbon steel, making it easier to deform during riveting. Coatings like zinc are often added for rust resistance.
Copper: Copper is chosen for its high electrical and thermal conductivity. It's soft and ductile, allowing for easy deformation and a secure fit in delicate materials.
Brass: Brass combines copper's corrosion resistance and zinc's strength. It's durable, malleable, and has an attractive appearance, making it great for decorative applications. Its non-sparking property is useful in flammable environments.
Conclusion
Rivets are a dependable alternative to bolts, nuts, screws, and welding, offering versatility across various industries. From the lightweight efficiency of aluminum rivets in aerospace to the corrosion-resistant durability of stainless steel in marine applications, rivets effectively meet diverse project demands—particularly for permanent installations. Their success largely depends on choosing the right material and a trusted manufacturer.
At HL Parts, we offer a wide range of CNC-machined metal rivets and provide customized precision CNC machining services to meet your specific project needs. Our skilled engineers, machinists, and quality control experts work collaboratively to deliver your product with precision and efficiency. For the best CNC-machined metal rivets and precision machining solutions, reach out to HL Parts today—we’re here to bring your projects to life!