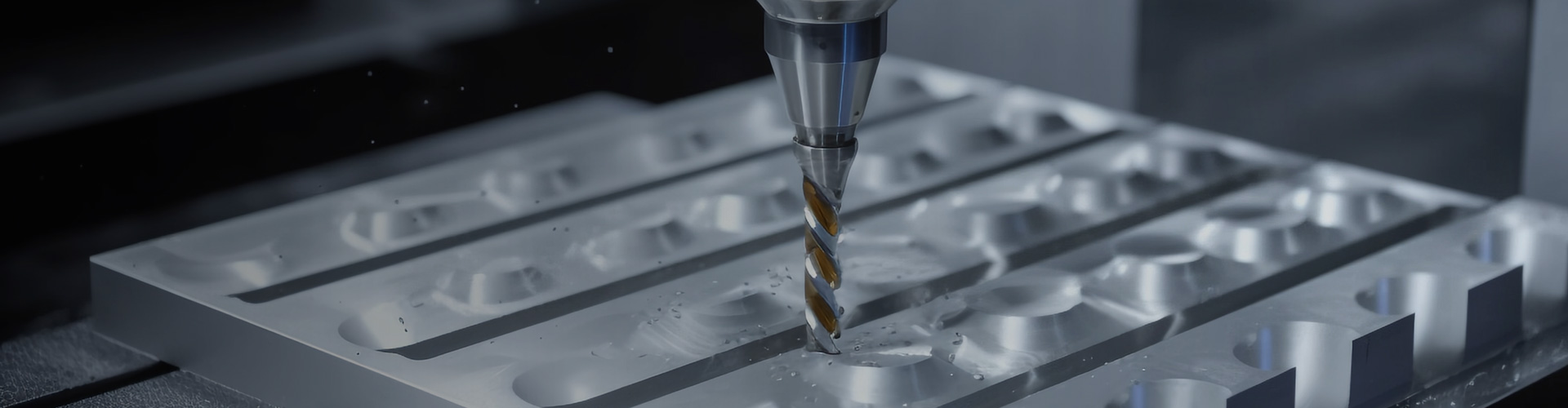
A Comprehensive Guide of Aluminum Anodizing
Aluminum anodizing stands as an electrochemical marvel, a process that transforms the surface of aluminum into a fortified, aesthetically pleasing layer. This transformative technique isn't just about looks; it significantly boosts the metal's durability and resistance to corrosion.
The Intricacies of Aluminum Anodizing
At its core, aluminum anodizing is an electrolytic procedure, typically carried out in a dilute sulfuric acid solution. When an electrical current courses through the aluminum part, a chemical reaction unfolds. Aluminum atoms on the surface shed electrons, becoming positively charged aluminum ions (Al³⁺). These ions then react with water molecules in the electrolyte, giving rise to a robust aluminum oxide layer. Unlike paint or plating, this oxide layer isn't merely a surface coating; it integrates seamlessly with the underlying aluminum, ensuring it won't chip or peel. Moreover, its porous structure opens the door to secondary treatments like coloring and sealing, expanding its functionality and aesthetic appeal.
The Step-by-Step Anodizing Process
Cleaning
The anodizing journey commences with meticulous cleaning. Grease, oil, dirt, and other contaminants have no place on the aluminum surface, as they can disrupt the anodizing process. To achieve a pristine surface, the aluminum is submerged in an alkaline or acid-based detergent bath, guaranteeing a clean slate for subsequent steps.
Pre-Treatment
Next up is pre-treatment, where the aluminum surface is primed for anodizing. Chemical pre-treatment involves etching with sodium hydroxide to smooth out irregularities and desmutting with nitric or sulfuric acid solutions to remove residues left behind by etching. Mechanical pre-treatment techniques, such as abrasive polishing, sandblasting, and shot peening, can also be employed to refine the surface texture as required.
Anodizing
After thorough rinsing, the prepped aluminum part is immersed in an electrolytic solution, usually sulfuric or chromic acid. Acting as the anode, the aluminum part, along with an inert cathode like stainless steel or lead, allows an electrical current to flow. This current triggers the formation of aluminum oxide, which deposits on the surface, creating a protective layer. Depending on the electrolyte, either a barrier oxide film (in neutral or slightly alkaline solutions) or a porous oxide film (in acidic solutions) forms. The thickness and properties of the porous oxide layer are influenced by factors like voltage, temperature, and anodizing duration.
Coloring (Optional)
For those seeking a splash of color, there are multiple options. Dyeing involves dipping the anodized part in an organic dye bath, where the dye seeps into the pores of the oxide layer. While cost-effective and offering a wide color palette, the resulting color may fade under UV exposure. Electrolytic coloring, on the other hand, submerges the part in a bath of metal salts and applies an electrical current, depositing metal ions into the pores and creating more UV-resistant colors.
Sealing
The final step, sealing, closes the pores in the anodized layer. This prevents further chemical reactions and locks in the color. Common sealing methods include immersion in boiling deionized water, steam sealing, or chemical sealing. Prompt sealing after coloring is crucial to maintain the quality and longevity of the anodized finish.
Types of Aluminum Anodizing
Chromic Acid Anodizing (Type I)
The oldest of the anodizing methods, Type I uses chromic acid as the electrolyte to form a thin oxide film (0.5 - 2.5 microns). Ideal for components with tight tolerances, it offers enhanced corrosion resistance and a non-reflective, matte finish, making it popular in military and aerospace applications. However, the toxicity of chromic acid raises environmental concerns, and its limited dye absorption can result in less vibrant colors.
Sulfuric Acid Anodizing (Type II)
The most widely adopted anodizing method, Type II uses sulfuric acid to produce a thicker oxide layer (2.5 - 25 microns). With superior abrasion and corrosion resistance, it's perfect for decorative applications, as it readily absorbs dyes, paints, and adhesives. It's also more cost-effective than Type I.
Hard Anodizing (Type III)
Similar to Type II in using sulfuric acid, Type III operates under more extreme conditions—lower temperatures, higher voltages, and increased current densities. This results in an extremely hard oxide layer exceeding 25 microns, providing excellent wear protection for industrial and mechanical parts. However, it's typically more expensive due to the stringent process requirements.
The Benefits of Anodizing Aluminum
Corrosion Resistance: The anodized layer shields aluminum from moisture, salt, and pollutants, making it a staple in architectural and marine applications.
Durability and Hardness: The aluminum oxide layer is much tougher than raw aluminum, ideal for high-use products like cookware and automotive components.
Aesthetic Versatility: Its ability to absorb dyes offers endless color possibilities, appealing to industries like consumer electronics and architecture.
Insulation: Improved thermal and electrical insulation makes it valuable in electronics and heat-resistant applications.
Adhesion: The anodized surface provides an excellent base for other coatings, enhancing product longevity.
Eco-Friendly: With minimal hazardous waste and recyclable properties, it aligns with sustainable manufacturing trends.
Design Considerations
Alloy Selection: Different aluminum alloys react differently to anodizing, so it's crucial to choose the right one for your application.
Tolerances: Account for dimensional changes caused by anodizing, especially in parts with tight tolerances.
Edge Design: Avoid sharp edges to ensure uniform anodizing and a better finish.
Combined Coatings: Consider combining anodizing with other coating technologies for enhanced performance.
Color and Aesthetics: Choose the right coloring method, consider color consistency, and select an alloy that responds well to dyeing for the desired look.
Conclusion
Aluminum anodizing has already established itself as a critical process in many industries, enhancing both the performance and appearance of everyday products. As technology advances, anodizing is set to play an even more important role in sustainable manufacturing, innovative material design, and emerging fields like nanotechnology and biomedicine.
At HL Parts, we specialize in providing top-quality aluminum anodizing services that are designed to meet your specific needs and help you stay ahead in a competitive market. Upload your file and let’s get started!