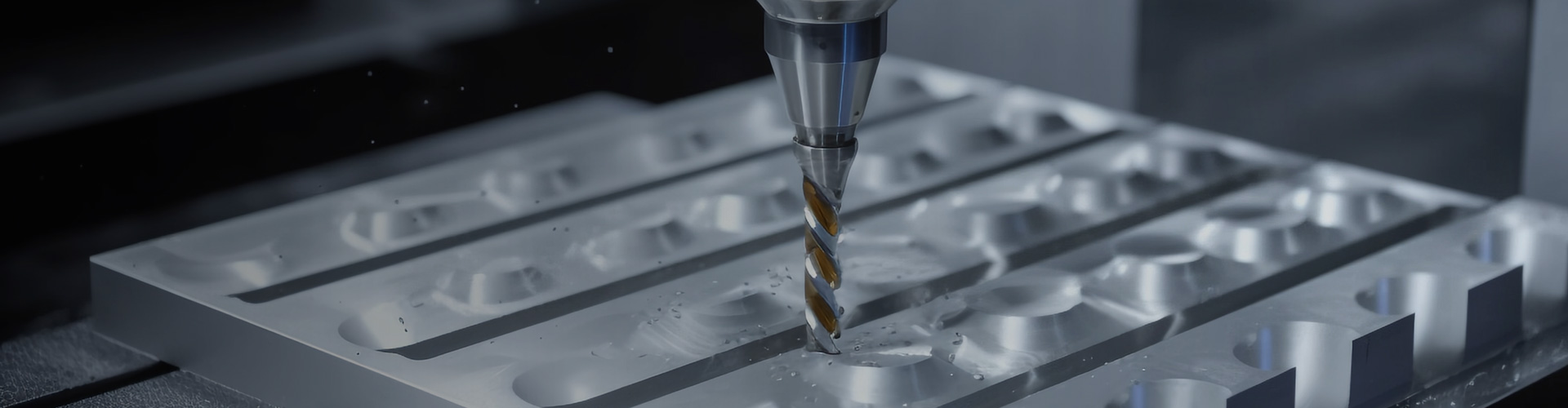
Exploring the Various Types of Screw Threads
In mechanics, the term "thread" typically refers to a screw thread, an essential element found in connectors, fasteners, and transmission systems. Screw threads are integral to a wide variety of components such as bolts, nuts, screws, and lead screws.
These components rely on screw threads for their intended functions. From industrial machinery to everyday household items, screw threads are an indispensable part of the systems that make many things work. Without them, most machines and devices would struggle to operate as intended.
But what exactly is a screw thread, and what are the various types? This article will delve into the details of screw threads, exploring their different forms and helping you choose the right type for your specific project.
What is a Screw Thread?
A screw thread is a helical ridge or groove that wraps around the circumference of a cylindrical or tapered surface. This spiral shape allows two or more components to be tightly joined through rotational movement or to convert rotational motion into linear motion.
The design of screw threads creates friction between the connected parts, facilitating a secure fastening or locking mechanism. Moreover, screw threads exhibit a self-locking feature, meaning the components won’t loosen on their own without external force being applied.
There are several types of screw threads, which are categorized according to various standards. Before diving into these types, let’s first understand some of the key geometric parameters that define a screw thread.
Essential Geometric Features of Screw Threads
Major Diameter (Outer Diameter)
The major diameter is the largest diameter, measured between the crests of the threads. This dimension is essential for determining the overall size and strength of the thread, influencing its tensile and shear performance. It also ensures that internal and external threads fit properly and engage effectively during assembly, securing the connection.
Minor Diameter (Inner Diameter)
The minor diameter is the smallest diameter, measured between the roots of the thread. It plays a crucial role in the strength and fit of the thread, impacting shear and fatigue strength. This diameter ensures proper engagement and compatibility between male and female threads, helping to maintain the integrity of the connection under load.
Pitch Diameter (Effective Diameter)
The pitch diameter is the diameter at which the width of the thread crest and root are equal. Located at the midpoint of the thread profile, it serves as the primary contact and load-bearing area for internal and external threads. This dimension is essential in determining the tightness of fit and the depth of engagement when a bolt and nut are mated, which directly influences load distribution across the threads. An accurate pitch diameter also enhances the self-locking properties of the thread.
Pitch and TPI
Pitch refers to the axial distance between adjacent thread crests, typically measured in millimeters (mm) for metric threads. It indicates the thread density and the distance the nut or bolt advances per rotation. You can quickly measure pitch using a Thread Pitch Gauge.
TPI (Threads Per Inch) is the number of thread crests within one inch, commonly used for imperial threads. Pitch and TPI are reciprocals of each other, meaning they are inversely related. A higher TPI corresponds to a finer pitch, and vice versa.
Lead
Lead is the distance a screw advances along its axis for each complete revolution. It indicates the efficiency of converting rotational motion into linear motion and plays a key role in load distribution and thread contact area. Smaller lead values generally result in a longer contact area, improving load capacity and wear resistance.
Helix Angle
The helix angle is the angle formed between the thread's helical path and a plane perpendicular to the thread axis. This angle affects both the efficiency of motion transfer and the choice of manufacturing methods. A larger helix angle improves transmission efficiency but may increase friction and wear.
Thread Angle
The thread angle is formed by the intersection of the thread flanks with a plane perpendicular to the screw’s axis. It is typically 60 degrees for standard thread designs, such as ISO metric and Unified Thread Standard (UTS) threads. The thread angle influences the mechanical properties of the thread, including strength, load distribution, and self-locking ability.
Tooth Angle
The tooth angle refers to the angle between the flanks of two adjacent threads. In thread applications, the tooth angle and thread angle are often the same, although in gear design, the tooth angle specifically refers to the profile angle of gear teeth, while the thread angle is used in thread applications.
How to Identify Thread Types?
Identifying thread types involves understanding the subtle differences in key geometric parameters discussed above. These small variations play a vital role in ensuring compatibility between threads and the equipment they are used with. To identify thread types accurately, you can follow a process that combines visual inspection, basic measurements, and standard comparison. This method allows you to confirm the correct thread type and ensure it meets the requirements of your application.
Step 1: Male Thread vs. Female Thread
First, identify whether the thread is male or female through observing the overall shape and structure of the thread. A male thread is an external helical ridge found on components such as bolts or screws, while a female thread is an internal helical groove present within nuts or holes.
Step 2: Tapered Thread vs. Parallel Thread
Next, determine whether the thread is tapered or parallel. A tapered thread features a gradually decreasing diameter along its length towards one end, while the diameter of a parallel thread remains constant throughout its length. This characteristic can sometimes be visually inspected, but if it's unclear, you can use a caliper for more precision. Measure the diameter at the first, fourth, and last full threads. If the measurements remain consistent, the thread is parallel. If the measurements show a decrease, it indicates a tapered thread.
Step 3: Measuring Thread Pitch
The next step in identifying your thread type is to determine the pitch size。Position the pitch gauge onto the thread and adjust it until it snugly fits between consecutive threads. Subsequently, read the indicated pitch value, which represents the precise distance between the threads.
Step 4: Measuring Thread Diameter
Once the pitch size is determined, the next step is to measure the thread diameter. It's important to note that the diameter measured may not exactly match the nominal size of the thread due to industry or production tolerances. Different diameter parameters require specific tools for accurate measurement. Here are some commonly used tools for measuring these parameters:
Major Diameter (Outer Diameter): This is the simplest parameter to measure directly and is typically done using external tools such as vernier calipers or micrometers.
Minor Diameter (Inner Diameter): The minor diameter requires more precision and is often measured with tools like an inside micrometer, bore gauge, or small hole gauge.
Pitch Diameter (Effective Diameter): Measuring the pitch diameter is more complex and often involves specialized gauges or indirect methods. Standard tools include thread ring gauges and thread plug gauges. For higher precision, a thread micrometer or the three-wire method is commonly used.
Step 5: Measuring Thread Angle
To measure the thread angle, use a thread angle gauge. Position the gauge along the thread flanks, ensuring it fits tightly to determine the angle between two adjacent thread flanks. Record the angle once measured.
Step 6: Verify Thread TypeFinally, using the measured diameter, pitch, and angle, consult standard thread charts or manuals provided later in this article to accurately identify the thread type.
Common Thread Standards and Thread Types
Thread classification is determined by various standards and specific application needs. For instance, pipe threads are designed for connecting pipes (such as BSP and NPT), while machine threads are used for general mechanical and structural connections (such as ISO and UTS). Below are some of the most common thread standards and types:
1. ISO Metric Thread Standard
Standard Numbers: ISO 68-1, ISO 261, ISO 965-1, ISO 965-2
The ISO metric thread standard is an internationally recognized system developed by the International Organization for Standardization (ISO). It utilizes the metric system for thread dimensions, with a thread angle of 60 degrees and diameters and pitches expressed in millimeters. Typical thread types under this standard include Coarse Thread and Fine Thread.
Coarse Thread | Fine Thread | ||||||
Thread Size (mm) | Pitch (mm) | Major Diameter (mm) | Minor Diameter (mm) | Thread Size (mm) | Pitch (mm) | Major Diameter (mm) | Minor Diameter (mm) |
M3 | 0.5 | 2.980 | 2.459 | M3*0.35 | 0.35 | 2.987 | 2.621 |
M4 | 0.7 | 3.978 | 3.342 | M4*0.5 | 0.5 | 3.978 | 3.242 |
M5 | 0.8 | 4.976 | 4.134 | M5*0.5 | 0.5 | 4.980 | 4.459 |
M6 | 1 | 5.974 | 4.917 | M6*0.75 | 0.75 | 5.978 | 5.188 |
M8 | 1 | 7.974 | 6.917 | M8*0.75 | 0.75 | 7.978 | 7.188 |
M10 | 1.5 | 9.968 | 8.376 | M10*0.75 | 0.75 | 9.978 | 9.188 |
M10*1 | 1 | 9.974 | 8.917 | ||||
M10*1.25 | 1.25 | 9.972 | 8.647 | ||||
M12 | 1.75 | 11.97 | 10.106 | M12*1 | 1 | 11.97 | 10.917 |
M12*1.25 | 1.25 | 11.97 | 10.674 | ||||
M12*1.5 | 1.5 | 11.97 | 10.376 | ||||
M16 | 2 | 15.96 | 13.835 | M16*1 | 1 | 15.97 | 14.917 |
M16*1.5 | 1.5 | 15.97 | 14.376 | ||||
M20 | 2.5 | 19.96 | 17.294 | M20*1 | 1 | 19.97 | 18.917 |
M20*1.5 | 1.5 | 19.97 | 18.376 | ||||
M20*2 | 2 | 19.96 | 17.835 | ||||
M24 | 3 | 23.95 | 20.752 | M24*1 | 1 | 23.97 | 22.917 |
M24*1.5 | 1.5 | 23.97 | 22.376 |
Coarse Thread is commonly used in various industrial and mechanical applications due to its ease of manufacturing and assembly. It is well-suited for general fastening tasks. On the other hand, Fine Thread is preferred for connections that demand higher strength and precision, offering improved locking performance in environments subject to substantial vibrations.
2. Unified Thread Standard (UTS)
Standard Number: ASME B1.1
The Unified Thread Standard is widely used in the United States and Canada. It also features a thread profile angle of 60 degrees, with diameters and pitches measured in inches. There are several series under UTS, including UNC (Unified National Coarse), UNF (Unified National Fine), and UNEF (Unified National Extra Fine).
UNC (2A) | UNF (2A) | ||||||
Nominal Size | Major Diameter (mm) | Minor Diameter (mm) | TPI | Nominal Size | Major Diameter (mm) | Minor Diameter (mm) | TPI |
1/4" x 20 UNC | 6.322 | 4.978 | 20 | 1/4" x 28 UNF | 6.325 | 5.360 | 28 |
5/16" x 18 UNC | 7.907 | 6.401 | 18 | 5/16" x 24 UNF | 7.910 | 6.782 | 24 |
3/8" x 16 UNC | 9.491 | 7.798 | 16 | 3/8" x 24 UNF | 9.497 | 8.382 | 24 |
7/16" x 14 UNC | 11.076 | 9.144 | 14 | 7/16" x 20 UNF | 11.079 | 9.728 | 20 |
1/2" x 13 UNC | 12.661 | 10.592 | 13 | 1/2" x 20 UNF | 12.667 | 11.328 | 20 |
5/8" x 11 UNC | 15.834 | 13.386 | 11 | 5/8" x 18 UNF | 15.839 | 14.351 | 18 |
3/4" x 10 UNC | 19.004 | 16.307 | 10 | 3/4" x 16 UNF | 19.012 | 17.323 | 16 |
7/8" x 9 UNC | 22.176 | 19.177 | 9 | 7/8" x 14 UNF | 22.184 | 20.269 | 14 |
1" x 8 UNC | 25.349 | 21.971 | 8 | 1" x 12 UNF | 25.354 | 23.114 | 12 |
2" x 4.5 UNC | 50.726 | 44.679 | 4.5 |
UNC is commonly used for general mechanical and structural connections, especially in applications with lower strength needs, such as construction frameworks and basic mechanical assembly. In contrast, UNF is designed for applications that require greater strength and precision, often used in industries like automotive and aerospace. For even higher precision and tighter tolerances, such as in high-precision instruments and small mechanical parts, UNEF is the preferred option.
3. British Thread Standard
Standard Number: BS 84, BS 2779 (ISO 228-1), BS 21 (ISO 7-1), BS 93
The British Standard Threads are mainly used in the UK and Commonwealth nations. These threads generally feature a 55-degree thread angle, with diameters and pitches measured in inches. Common types include:
● British Standard Whitworth Thread (BSW): Developed by Joseph Whitworth in 1841, BSW was the first standardized thread form and was widely used in the UK and former British colonies. It has a 55-degree thread angle with rounded crests and roots. BSW threads are primarily used in general mechanical engineering and construction, suitable for rougher machining conditions.
● British Standard Fine Thread (BSF): A variant of BSW, BSF threads also have a 55-degree angle but with a finer pitch, making them ideal for applications requiring stronger connections and tighter fits.
● British Standard Pipe Thread (BSP): BSP threads are used for pipe connections and feature a 55-degree angle. There are two main variations: BSPP (parallel threads) and BSPT (tapered threads). BSPP threads are typically sealed using a sealing face or O-ring, commonly found in hydraulic and pneumatic systems. BSPT threads rely on thread interference to create a seal, making them suitable for high-pressure piping systems.
● British Association Thread (BA): These threads have a 47.5-degree angle and are predominantly used in small screws and bolts. BA threads are commonly found in electronics and precision engineering.
4. National Pipe Thread (NPT)
Standard Number: ANSI/ASME B1.20.1
The National Pipe Thread (NPT) is a tapered thread standard commonly used in the United States and other regions. It has a 60-degree thread angle with a taper of 1/16 inch per inch. NPT threads form a seal through thread interference, making them suitable for high-pressure piping systems, industrial equipment, and plumbing applications in buildings.
(table3)
5. Right-Hand Threads (RH) and Left-Hand Threads (LH)
A thread is called a right-hand thread if it tightens when turned clockwise. It is the most common thread direction used in most applications. Conversely, a left-hand thread tightens when turned counterclockwise. Left-hand threads are always used in situations where it is important to prevent the thread from loosening due to self-movement, such as with the left-hand bicycle pedal.
6. “V” Shape Threads
These threads feature a triangular or V-shaped cross-section with a 60-degree included angle. This thread form is the most commonly used due to its versatility and ease of manufacture. "V" shape threads are suitable for both general-purpose fastening and load-bearing applications. Notable examples include Unified Thread Standard (UTS) and ISO metric threads.
7. Square Threads
Square threads have a square cross-section, which makes them more challenging to fabricate compared to “V” shape threads. They offer lower friction and wear due to the perpendicular thread flanks, which provide more even load distribution and reduce the likelihood of jamming under heavy loads. Square threads are ideal for high-efficiency applications that involve transmitting large forces, such as lead screws and jack screws.
8. Acme Threads
Acme threads are a variation of square threads that are easier to produce. They have a trapezoidal profile with a 29-degree thread angle. Their broader, more stable cross-sectional design makes them stronger under load than square threads. Acme threads are commonly used in applications requiring strength and precision, including brass valves, bench vices, and screw-cutting lathes.
9. Knuckle Threads
Knuckle threads have a rounded top and bottom, offering excellent resistance to damage and wear by reducing sharp edges. This design minimizes wear and tear and prevents the accumulation of dirt and debris. Knuckle threads are ideal for applications where threads are frequently engaged and disengaged or exposed to harsh environments.
They are often used in industries such as railways and heavy machinery, where robustness and durability are essential, and in components like couplings, lids, and covers that require repeated screwing and unscrewing.
10. Buttress Threads
Buttress threads are designed to handle high axial thrust in one direction. Their profile features a nearly perpendicular load-bearing face and a slanted trailing face, typically at a 45-degree angle. This design allows for efficient force transmission along the screw's axis while minimizing thread deformation. Buttress threads are used in applications requiring significant load-bearing strength in one direction, such as hydraulic presses, vices, lifting equipment, and machinery dealing with heavy loads or high pressure.
11. Worm Threads
Worm threads are used in worm gears, which transmit motion and power between non-intersecting, perpendicular shafts. The worm, featuring worm threads, meshes with a worm wheel to provide smooth and continuous motion. This type of gear system offers high reduction ratios, enabling substantial speed reduction and torque multiplication. Worm threads are widely used in applications like conveyor systems, lifts, steering mechanisms, and machinery requiring precise control and high torque. Their self-locking feature also prevents back-driving under certain conditions, enhancing safety and control.
12. Single and Multi-Threads
Single threads consist of a single helical ridge. With each full rotation, the screw advances by a distance equal to one pitch length. This design strikes a balance between strength and ease of manufacturing, making it the most common and straightforward thread type.
Multi-threads, on the other hand, feature two or more helical ridges. This allows the screw to advance by multiple pitch lengths with each rotation. For example, double-start threads have two helical ridges, so the screw moves forward by two pitch lengths per turn. This design reduces the time and effort needed to achieve the same linear motion, making it ideal for applications requiring rapid movement, such as high-speed machinery, actuators, and precision instruments.
Conclusion
There are numerous thread types, each designed to meet specific functional and manufacturing needs. When designing products, it’s important to choose the right thread type based on your requirements. We hope this guide has helped you better understand the different thread types and how to select the best one for your mechanical and engineering projects.
At HL Parts, we specialize in CNC-machined fasteners, offering a range of thread types and processing methods tailored to different materials. Our engineering team, with over 10 years of industry experience, ensures that all products undergo rigorous testing to maintain the highest quality. Let us help you find the right thread solutions for your project. Simply upload your CAD file, and we’ll work closely with you to bring your designs to life.