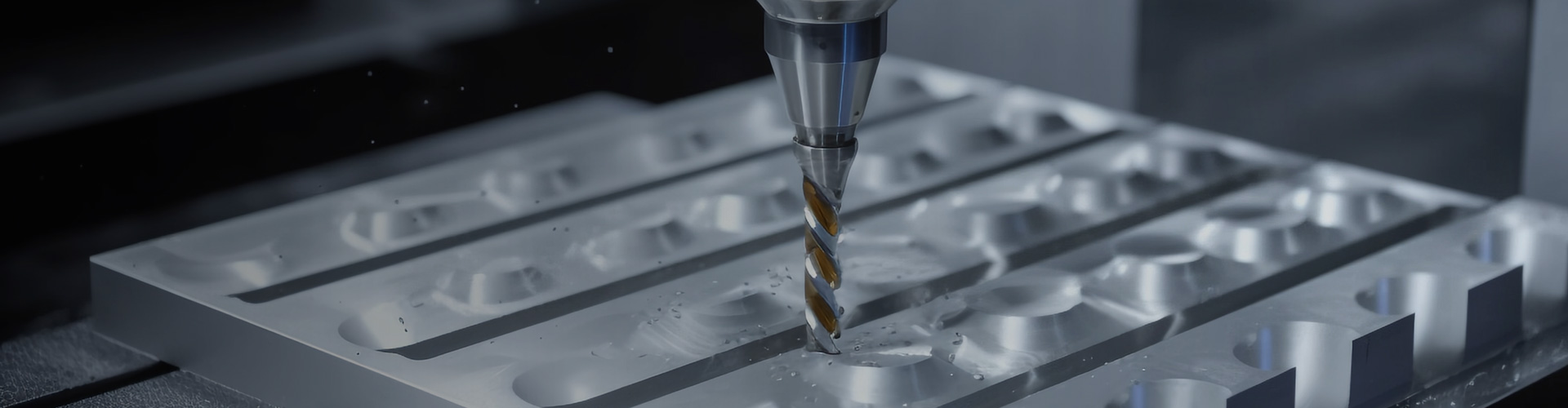
What is CNC Turning? A Guide to Precision Machining
What is CNC Turning?
CNC turning is a subtractive manufacturing process where a cutting tool removes material from a rotating workpiece to create cylindrical, conical, or axisymmetric parts. The process is controlled by computer numerical control (CNC), ensuring high precision and repeatability.
- CNC (Computer Numerical Control): Uses programmed instructions (G-code) to automate machining operations.
- Turning: A lathe-based process where the workpiece rotates while a stationary or moving tool shapes it.
CNC turning is performed on CNC lathes or more advanced CNC turning centers, which can include live tooling for milling and drilling.
CNC Turning vs. CNC Milling: Key Differences
While both are CNC machining processes, they differ in workpiece movement and cutting approach:
- CNC Turning: The workpiece rotates, and the tool moves linearly (ideal for cylindrical parts).
- CNC Milling: The cutting tool rotates, and the workpiece remains stationary (better for complex 3D shapes).
Turning is best for: Shafts, bushings, threaded rods, and other rotationally symmetric parts.
Milling is best for: Complex geometries, slots, pockets, and non-symmetrical components.
How CNC Turning Works: Step-by-Step Process
1. Design & Programming
- Engineers create a 3D model (CAD) and convert it into machine instructions (CAM).
- Critical parameters:
- Cutting speed (SFM): Surface speed of the rotating workpiece (m/min or ft/min).
- Feed rate: Tool advancement per revolution (mm/rev or in/rev).
- Depth of cut: Determines material removal rate.
2. Machine Setup
- The workpiece is clamped in a chuck or collet.
- Cutting tools are loaded into the turret (indexable tool holder).
- The CNC program (G-code) is loaded into the machine controller.
3. Machining Execution
- The spindle rotates the workpiece at high speed.
- The turret positions tools for operations like facing, turning, drilling, or threading.
- Multiple passes may be required for roughing and finishing.
4. Post-Processing
- Parts may undergo deburring, polishing, or inspection for final quality.
Common CNC Turning Operations
1. Straight Turning (Roughing & Finishing)
- Reduces the workpiece diameter to near-final dimensions.
- Roughing: High material removal with lower precision.
- Finishing: Fine cuts for tight tolerances and smooth surfaces.
2. Taper Turning
- Produces conical shapes by angling the cutting tool.
3. Facing
- Creates a flat surface perpendicular to the rotational axis.
4. Drilling & Boring
- Drilling: Creates center holes.
- Boring: Enlarges or refines existing holes.
5. Threading
- Cuts internal (tapped) or external (threaded rod) screw threads.
6. Grooving & Parting
- Grooving: Cuts narrow channels (e.g., for O-rings).
- Parting (Cutoff): Separates finished parts from the stock.
7. Knurling
- Adds textured grip patterns (common in handles and knobs).
Types of CNC Turning Machines
1. Horizontal CNC Lathes
- Most common type, suitable for general-purpose turning.
- Workpiece rotates horizontally.
2. Vertical CNC Lathes
- Workpiece rotates vertically, ideal for heavy or large-diameter parts.
3. CNC Turning Centers
- Advanced machines with live tooling (can perform milling & drilling).
- Multi-axis capabilities for complex geometries.
4. Swiss-Type Lathes
- Specialized for ultra-precise, small-diameter parts (e.g., medical screws).
Advantages of CNC Turning
✔ High Precision (±0.02 mm tolerance achievable)
✔ Fast Production (Automated, repeatable processes)
✔ Material Versatility (Metals, plastics, composites)
✔ Complex Feature Machining (Threads, tapers, grooves)
✔ Scalability (Suitable for prototyping & mass production)
Limitations of CNC Turning
✖ Limited to Rotational Symmetry (Not ideal for complex 3D shapes)
✖ Size Constraints (Large parts may require specialized machines)
✖ Higher Initial Cost (Compared to manual lathes)
Is CNC Turning Right for Your Project?
Best for:
- Cylindrical/conical parts (shafts, bushings, fittings).
- High-precision components (medical, aerospace, automotive).
- Medium-to-high production runs.
Not Ideal for:
- Non-symmetrical parts (better suited for CNC milling).
- Very large or heavy components (may need custom setups).
- Low-volume prototypes (3D printing may be cheaper).
Conclusion
CNC turning is a highly efficient and precise machining method for rotationally symmetric parts. By understanding its capabilities, operations, and machine types, manufacturers can determine whether it aligns with their production needs. For complex geometries, combining CNC turning with milling (via turning centers) provides greater flexibility.
For optimal results, consult with machining experts to select the right process, materials, and tolerances for your project.
Order With HL Parts for Your Custom CNC Turned Parts
Now that you've obtained detailed information about CNC turning, if you're searching for the right partner for your project, look no further than HL Parts. As an ISO 9001:2015 certified facility with nearly two decades of machining experience,we ensure that your products meet the highest quality standards—all at competitive prices.
We offer on-demand manufacturing solutions tailored to your specific needs, with expert support available 24/7—from design to delivery. Upload your CAD file today to receive a free DFM analysis and take the first step toward bringing your project to life!