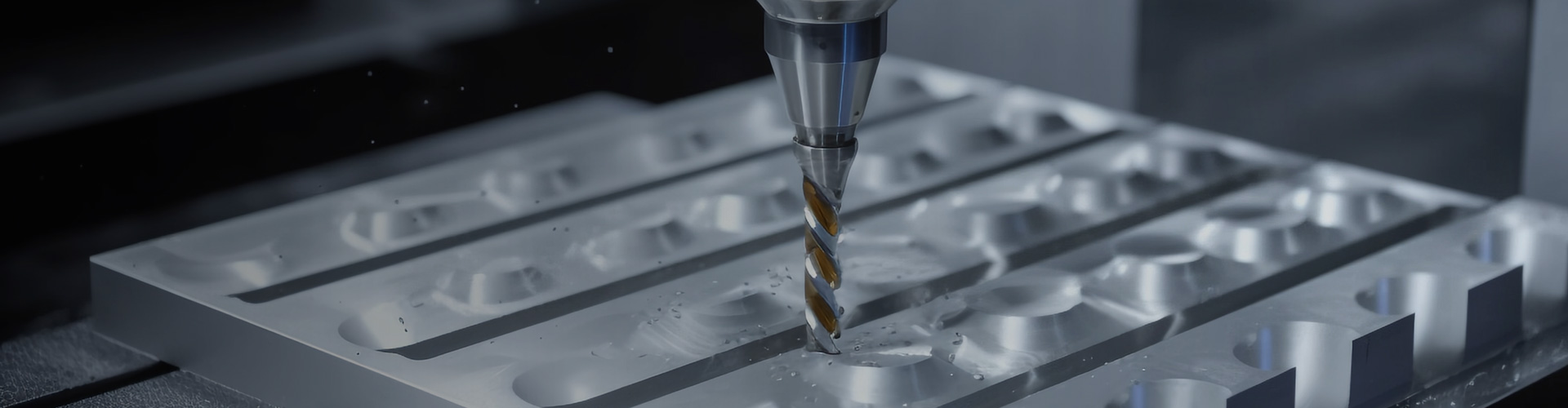
CNC Machining Costs: Key Factors and Cost-Saving Strategies
CNC machining has become a cornerstone of modern manufacturing, prized for its unparalleled precision and efficiency. If you're planning to utilize CNC machining for your products, a pivotal question looms large: what will the costs entail, and will they align with your budget? The truth is, there's no universal price tag for CNC machining. Its costs are shaped by numerous factors that can have a substantial impact on the final expenditure.
This guide will delve into the critical elements influencing CNC machining costs and offer practical strategies to help you cut down expenses while still ensuring top-notch product quality.
Key Factors Shaping CNC Machining Costs
CNC machining costs fluctuate widely based on aspects like materials, labor, equipment, and other project-specific details. Many companies rely on a basic formula to calculate costs:
Total Cost = Raw Material Cost + Machining Cost + Post-Processing Cost + Shipment Cost + Profit Margin
Let's take a closer look at each of these components.
Raw Material Cost
The raw material cost is the bedrock of CNC machining expenses. The material you choose can greatly affect the overall cost. Two key aspects help explain the composition of raw material costs and why some materials are pricier than others:
· Inherent material cost: This is the base price of the material, which is determined by factors such as its application, market supply and demand, and production costs. Premium materials like titanium alloys, stainless steel, and engineering plastics like PEEK and PTFE usually come with a heftier price tag compared to common materials like aluminum, mild steel, or ABS plastic. Special-purpose materials used in aerospace or medical fields are even more expensive due to strict quality requirements. Some materials also demand specialized manufacturing or processing methods. For example, engineering plastics like PEEK and PTFE need to be produced under high temperatures and pressures, driving up their production costs. In contrast, materials like aluminum and mild steel benefit from well-established, large-scale manufacturing processes, making them more cost-effective.
· The Machinability of Material: Machinability refers to how easily a material can be processed during machining. Materials with good machinability, such as aluminum and certain plastics, enable efficient processing, minimize tool wear, and make it easier to control the surface finish, helping to reduce machining costs. Conversely, harder-to-machine materials like titanium alloys, stainless steel, and high-strength alloys take more time, require specialized tools, and need advanced processes, all of which drive up machining costs.
Machining Cost
Machining costs are generally calculated using the formula:
Machining Costs = Hourly Rate x Machining Time
· Hourly Rate: The hourly rate in CNC machining represents the cost of using a machine or equipment per hour. It typically includes several components:
· Equipment Cost: The purchase price and depreciation of CNC machines influence the hourly rate. More complex multi-axis machines usually have higher rates because of their advanced capabilities.
· Tooling and Consumables: The frequency of tool use, wear, and expenses for consumables like cutting fluids impact the hourly rate. Hard-to-machine materials often call for higher-quality tools, increasing costs.
· Labor Cost: The wages of CNC machine operators are factored into the hourly rate. Labor charges are incurred during the design phase, machine setup, and any post-processing operations like secondary finishing. More complex operations often require more skilled operators, resulting in higher labor costs.
· Maintenance and Operating Costs: Regular machine maintenance, electricity, space rental, and other operational expenses are also part of the hourly rate.
In China, simpler machines like 3-axis CNC mills, which are suitable for basic tasks, typically have an hourly rate of
20. CNC lathes, which are generally easier to operate, have an hourly rate around
25 to $30 per hour or more. These rates are much higher in the European or US markets, making outsourcing CNC machining projects to China a cost-effective choice.
· Machining Time: Machining time is the total duration needed to complete a part, including both setup time and actual machine operation time. It's another crucial factor affecting overall machining costs.
· Setup Time: Setup time covers the preparatory work before machining starts. Every CNC - machined part begins with a 3D model, usually designed by experts using CAD (Computer-Aided Design) software. The resources used to create this 3D model contribute significantly to the setup costs. Setup costs also include optimizing the design and preparing the model for manufacturing using CAM (Computer-Aided Manufacturing) software.
· Machine Operation Time: This is the time the machine runs to cut and shape the material into the final part. Complex designs and hard-to-machine materials will increase operation time, thereby driving up machining costs.
Post-Processing Cost
After machining, parts may need additional processes like assembly or surface finishing (such as polishing, powder coating, anodizing). These extra steps add to the overall machining costs due to the additional labor, time, and materials involved.
Shipment Cost
Transporting the finished parts to their destination, including packaging and logistics, contributes to the total expenses. Faster shipping options may be more expensive but are sometimes necessary for urgent orders.
Profit Margin
Like any business, suppliers and vendors include a profit margin to cover overhead costs and ensure profitability. This margin is essential for maintaining operations and making future investments in technology and capabilities. The profit margin varies depending on market conditions, competition, and project complexity.
Typically, CNC machining companies aim for a profit margin of 10% to 20% per order. However, this rate can vary widely among suppliers. Some parts may command higher margins, especially those that require specialized skills or intricate finishes. For example, highly detailed appearance models often have higher profit margins than standard structural components because of the additional expertise and precision needed. In the end, suppliers need to strike a balance between profitability and competitive pricing to keep providing high-quality services and stay viable in the market.
Strategies to Lower CNC Machining Costs
Now that we understand the main factors affecting CNC machining costs, it's clear that there are many ways to optimize and save money without sacrificing quality. By focusing on key areas, you can identify opportunities to reduce expenses. Here are some practical tips to help you cut down on your CNC machining costs.
· Optimize Design for Manufacturability (DFM): Design optimization is one of the most effective ways to reduce CNC machining costs. Thoughtful design choices can significantly cut down machining time, minimize tool wear, and avoid unnecessary costs associated with complex processes.
· Reduce Complex Geometries: Complex shapes often require advanced multi-axis CNC machines, which increase setup time, machining complexity, and cost. Features like undercuts, internal cavities, or intricate curves may need specialized tooling or additional setups. Simplify part geometry whenever possible, or consider breaking complex parts into simpler subcomponents that can be machined separately and assembled later.
· Eliminate Unnecessary Features: Review your design for any features that don't contribute to the part's function or performance. Removing non-essential elements can reduce the number of operations needed, cutting down both setup and machining time.
· Design for Standard Tooling: Where feasible, design parts that can be machined using standard tooling sizes and shapes. This allows machinists to use readily available tools, reducing both setup time and the need for custom tools.
· Minimize Tight Tolerances: Tight tolerances require precise machining, slower cutting speeds, and more finishing passes, all of which increase time and tool wear. Only specify tight tolerances when necessary, such as for critical mating parts. For non-critical dimensions, looser tolerances can reduce machining time and lower production costs.
· Consider Part Orientation: The orientation of your part during machining can affect the number of setups required and the complexity of the fixturing. Multiple setups usually mean more labor and time. Design parts to minimize the number of required setups. Parts that can be machined in a single setup are more cost-efficient as they reduce the time spent repositioning the part and adjusting fixtures.
· Select the Right Material: When performance requirements allow, choose materials with good machinability. Aluminum is a popular choice due to its excellent machinability, lightweight nature, and good strength-to-weight ratio. Softer plastics like ABS and nylon are also easy to machine and can be a cost-effective option for non-structural components.
Harder materials like stainless steel, titanium, and certain alloys pose more challenges during machining. They tend to wear out tools faster and may require specialized cutting tools, leading to more frequent tool changes and increased maintenance costs.
· Manufacturing Process Optimization: Process optimization is another effective way to reduce machining costs. Programming efficient tool paths and optimizing machining parameters such as cutting speed, feed rate, and cutting depth can minimize cutting time and reduce tool wear. This not only boosts overall efficiency but also extends tool life, reducing the frequency of tool replacements and cutting costs.
Implementing automatic tool changers (ATC) and standardized fixtures can cut setup and changeover times, speeding up production and avoiding wasted time on frequent adjustments. Analyzing and optimizing the entire production process to eliminate bottlenecks and inefficiencies ensures smooth transitions between operations, further increasing production efficiency and reducing downtime.
· Avoid Multiple Surface Finishes: Avoiding multiple surface treatments can significantly cut down CNC machining costs. During the design phase, choosing materials with good surface finish and durability, such as aluminum, can reduce the need for additional surface treatments. These materials often have an ideal surface quality right after machining, eliminating the need for extra processing. Using the "as-machined" finish whenever possible is the most cost-effective option as it skips unnecessary additional steps.
While surface treatments like chemical plating, sandblasting, electro-polishing, or anodizing may be needed to enhance specific properties of a component, they should only be used when absolutely necessary. Also, avoid using different surface finishes on various parts of a single component. Maintaining consistent surface treatment standards across all surfaces can simplify setup, reduce process changes, and lower costs further.
· Leverage Batch Production: Every CNC machining job requires a setup phase, including configuring machines, preparing tools, and loading programs. This setup time incurs a fixed cost, whether you're producing one part or a thousand. By choosing larger batch production, you can spread this setup cost over more parts, significantly reducing the cost per unit. This is especially beneficial for complex setups that require specialized jigs, fixtures, or multiple machine calibrations.
CNC shops often offer volume discounts for larger orders. Batch production allows the shop to run machines more efficiently, minimizing downtime between jobs. Bulk material purchases for larger orders can also lead to cost savings, which are often passed on to the customer.
· In-house vs. Outsource: Deciding between in-house production and outsourcing is a key factor in reducing CNC machining costs. In-house production gives you more control over quality and flexibility but requires significant upfront investments in equipment, skilled labor, and ongoing maintenance. This approach can be cost-effective for large-scale or long-term projects where the initial costs can be amortized over time.
Outsourcing, on the other hand, shifts the burden of equipment and labor costs to a specialized service provider, allowing you to pay only for the machining services you need. Outsourcing can be particularly advantageous for small to medium production runs or when specialized capabilities are required without a large capital investment.
Order With HL Parts for Outsourcing Components
Choosing the right outsourcing partner can make all the difference in reducing CNC machining costs while ensuring high quality. HL Parts offers precision CNC machining services with competitive pricing and exceptional standards. As a trusted provider in China, we leverage the region's lower operational costs to deliver top-quality results at a fraction of the price found in developed countries.
At HL Parts, we handle everything from prototyping to large-scale production, helping you streamline operations and focus on your core business. Our dedicated engineering team quickly reviews your designs and provides valuable feedback to ensure a smooth project from start to finish. Meanwhile, our logistics team ensures the most effective lead times in the industry, guaranteeing timely delivery of your products.Start your CNC machining project with HL Parts today and enjoy the benefits of cost-effective and reliable outsourcing.