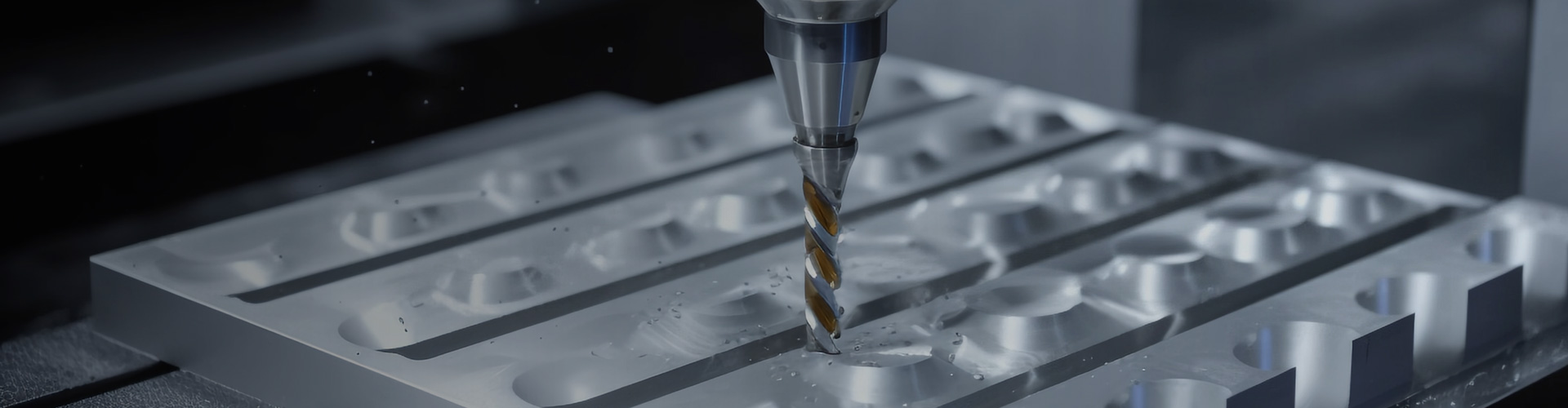
The Differences Between 5-Axis and 3+2 Axis Machining
Introduction: The Evolution of Multi-Axis Machining in Modern Industry
As manufacturing requirements become increasingly sophisticated, with demands for complex geometries, tighter tolerances, and advanced materials, traditional 3-axis CNC machining often falls short. This has led to the rapid advancement of multi-axis CNC technology, with machines now capable of controlling up to 12 axes simultaneously. Among these, 5-axis CNC machining stands out as the most widely adopted solution, offering unparalleled precision and flexibility.
However, not all 5-axis machining is the same. There are two primary types:
1. Simultaneous 5-axis machining (full continuous 5-axis)
2. 3+2 axis machining (positional 5-axis)
Many manufacturers and engineers confuse these two methods. Do they operate the same way? If not, what are their key differences? This in-depth guide will clarify these questions, helping you choose the best approach for your machining needs.
Understanding Simultaneous 5-Axis Machining
What Is Simultaneous 5-Axis Machining?
Simultaneous 5-axis machining, also called full continuous 5-axis, is an advanced CNC process where all five axes move at the same time during cutting operations. This allows the tool to approach the workpiece from any angle, enabling the machining of highly complex shapes in a single setup.
The Five Axes in Simultaneous 5-Axis Machining
1. Linear Axes (X, Y, Z)
- X-axis: Left-to-right movement
- Y-axis: Front-to-back movement
- Z-axis: Up-and-down movement
2. Rotational Axes (A, B, or C, depending on machine configuration)
- A-axis: Rotation around X (tilting forward/backward)
- B-axis: Rotation around Y (tilting side-to-side)
- C-axis: Rotation around Z (360-degree swiveling)
The exact configuration varies by machine, but the key advantage is that all five axes move dynamically, allowing for freeform contouring, undercuts, and deep cavities without repositioning the workpiece.
How It Works
- The CNC controller coordinates simultaneous movement of all five axes.
- The cutting tool dynamically adjusts its angle to maintain optimal contact with the workpiece.
- This eliminates multiple setups, reducing errors and improving efficiency.
Understanding 3+2 Axis Machining (Positional 5-Axis)
What Is 3+2 Axis Machining?
Unlike simultaneous 5-axis machining, 3+2 axis machining, also called positional 5-axis, locks the two rotational axes once the workpiece is positioned. The actual cutting is then performed using only the X, Y, and Z linear axes, similar to traditional 3-axis machining.
Key Characteristics of 3+2 Axis Machining
1. Rotational axes position the workpiece but remain fixed during cutting.
2. Machining occurs along three linear axes (X, Y, Z).
3. Ideal for angled features but not for freeform surfaces.
Advantages Over Traditional 3-Axis Machining
- Shorter, stiffer tools can be used (reducing vibration).
- Better access to steep walls and deep cavities.
- Reduced setup time compared to multiple 3-axis operations.
5-Axis Versus 3+2 Axis Machining: Key Differences
Advantages and Disadvantages of Each Method
Simultaneous 5-Axis Machining: Pros and Cons
Advantages:
1. Unmatched geometric complexity (undercuts, organic shapes).
2. Single-setup machining (reduces errors and speeds production).
3. Superior surface finish (less post-processing needed).
4. Greater innovation potential (ideal for aerospace, medical, automotive).
Disadvantages:
1. Higher machine and maintenance costs.
2. Complex programming and skilled operators required.
3. Not always necessary for simpler parts.
3+2 Axis Machining: Pros and Cons
Advantages:
1. More affordable than full 5-axis.
2. Simpler programming (similar to 3-axis).
3. Reduced vibration (due to locked rotational axes).
4. Faster for angled features and molds.
Disadvantages:
1. Limited for freeform surfaces.
2. May require multiple setups.
3. Less smooth surface finish (blend lines may appear).
Which One Should You Choose?
Choose 3+2 Axis Machining If:
1. Cost is a primary concern.
2. You need angled features but not freeform shapes.
3. You're upgrading from 3-axis machines.
Choose Simultaneous 5-Axis Machining If:
1. You need complex, organic geometries.
2. Surface finish and precision are critical.
3. You want to minimize setups and handling time.
Why Partner with HL Parts for 5-Axis CNC Machining?
At HL Parts, we specialize in high-precision CNC machining, offering:
1. Advanced 3-axis, 4-axis, and 5-axis CNC Machining Service.
2. Expert engineering support (10+ years of experience).
3. Fast turnaround and competitive pricing.
Upload your design today for a free DFM analysis and quote!
By understanding the differences between simultaneous 5-axis and 3+2 axis machining, you can make an informed decision that optimizes cost, efficiency, and precision for your project.
Upload your CAD files now to discuss your CNC machining needs.