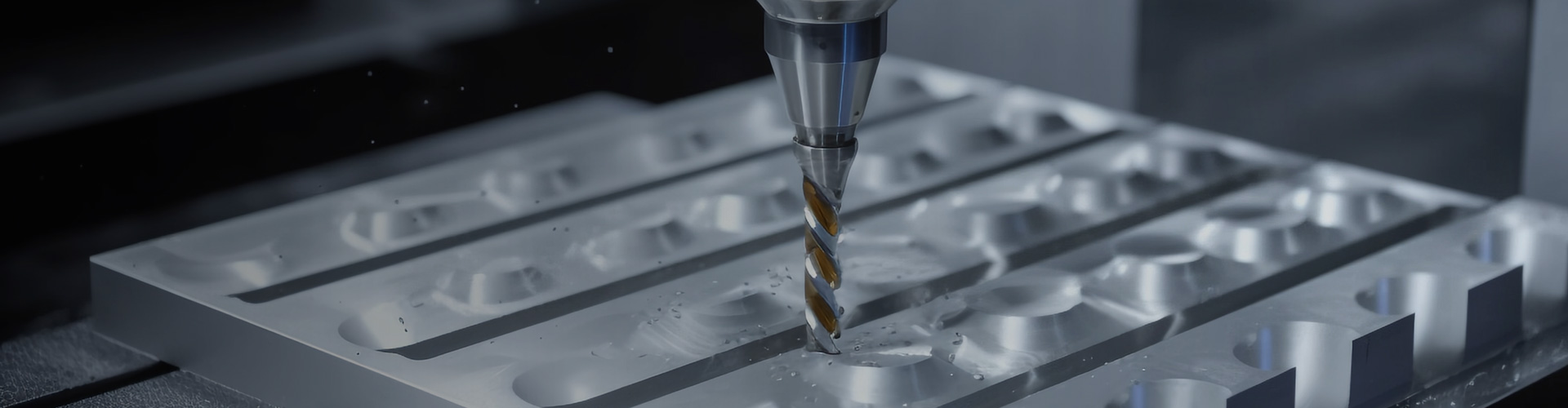
5-axis CNC Machining - Revolutionizing Precision Manufacturing
Introduction to 5-Axis CNC Machining in Industry 4.0
In the rapidly evolving landscape of Industry 4.0, Computer Numerical Control (CNC) machining has emerged as a fundamental pillar of modern manufacturing. By leveraging computerized controls to operate machine tools, CNC technology has transformed traditional machining processes, delivering unprecedented levels of precision, efficiency, and repeatability. However, as industries demand increasingly intricate and high-tolerance components, conventional 3-axis and 4-axis CNC machining often struggle to meet these advanced requirements.
This is where 5-axis CNC machining steps in as a game-changer. By integrating two additional rotational axes alongside the standard three linear axes, 5-axis CNC machines enable the cutting tool to approach the workpiece from nearly any angle. This enhanced flexibility eliminates the need for multiple setups, significantly boosts productivity, and allows for the creation of highly complex and aesthetically refined parts—unlocking new possibilities for manufacturers worldwide.
This comprehensive guide will explore what 5-axis CNC machining is, how it operates, the mechanics of its five axes, its advantages, and its limitations.
Understanding 5-Axis CNC Machining
Defining Axis Count in CNC Machining
Before delving into 5-axis machining, it’s essential to clarify what "axis count" means in CNC operations. An axis refers to a direction in which the cutting tool (or workpiece) can move to shape the material. The more axes a CNC machine has, the greater its range of motion, enabling the production of more sophisticated geometries with tighter tolerances.
How 5-Axis CNC Machining Differs from Traditional Methods
5-axis CNC machining involves the simultaneous movement of the cutting tool or workpiece along five distinct axes. Unlike 3-axis machining, which operates along the X, Y, and Z linear axes, 5-axis machines incorporate two additional rotational axes, allowing for:
- Multi-surface machining in a single setup
- Enhanced precision for complex curves and contours
- Reduced manual intervention and setup time
This makes 5-axis CNC machining ideal for producing aerospace components, medical implants, automotive parts, and intricate molds.
The Five Axes of CNC Machining: Linear and Rotational Movements
1. Linear Axes (X, Y, Z)
These are the foundational axes present in all CNC machines:
- X-axis: Left-to-right movement (parallel to the worktable)
- Y-axis: Front-to-back movement (parallel to the worktable)
- Z-axis: Up-and-down movement (parallel to the spindle)
These axes allow for basic milling, drilling, and cutting operations.
2. Rotational Axes (A, B, C)
5-axis CNC machines add two rotational axes to the standard three linear axes. Depending on the machine configuration, these can be any two of the following:
- A-axis (rotation around X): Typically tilts ±120° to ±150°, with some high-end models achieving ±180°
- B-axis (rotation around Y): Similar range as the A-axis
- C-axis (rotation around Z): Often provides full 360° continuous rotation
The combination of these axes varies based on the machine type, leading to different machining capabilities.
How 5-Axis CNC Machining Works: Step-by-Step Process
Step 1: CAD/CAM Design & Preparation
- Engineers create a 3D model of the part using CAD (Computer-Aided Design) software.
- The design is then converted into machine-readable instructions (G-code) via CAM (Computer-Aided Manufacturing) software, defining toolpaths, cutting speeds, and feed rates.
Step 2: Machine Setup & Workpiece Alignment
- The workpiece is securely fixtured on the machine table.
- Appropriate cutting tools are selected and loaded into the automatic tool changer (ATC).
Step 3: Machining Execution
- The CNC control system interprets the G-code and coordinates simultaneous movement across all five axes.
- The three linear axes (X, Y, Z) move the tool or workpiece in straight lines.
- The two rotational axes (A/B, A/C, or B/C) allow for tilting and rotating, enabling complex cuts.
Step 4: Real-Time Monitoring & Adjustments
- Operators oversee the process, ensuring smooth operation.
- Adjustments to cutting parameters or toolpaths can be made to optimize performance.
Types of 5-Axis CNC Machines
Depending on how the rotational axes are configured, 5-axis CNC machines fall into three main categories:
1. Table/Table Configuration
- Both rotational axes are on the worktable.
- Ideal for small to medium-sized parts with complex geometries.
- Limitation: Lower load capacity, not suitable for heavy workpieces.
2. Head/Head Configuration
- Both rotational axes are on the spindle head.
- Best for large, heavy parts since the workpiece remains stationary.
- Limitation: Restricted rotational range compared to table-based machines.
3. Head/Table (Hybrid) Configuration
- One rotational axis on the spindle, the other on the table.
- Offers greater flexibility for undercuts and multi-sided machining.
- Limitation: Workpiece size may be constrained by table rotation limits.
Advantages of 5-Axis CNC Machining
1. Unmatched Geometric Complexity
- Can produce deep cavities, undercuts, and freeform surfaces that are impossible with 3-axis machining.
2. Superior Precision & Efficiency
- Single-setup machining reduces errors and speeds up production.
- Tolerances can be held within micrometer-level accuracy.
3. Exceptional Surface Finish
- Optimal tool positioning minimizes tool marks and vibrations.
- Reduces the need for secondary finishing operations.
4. Reduced Fixturing & Tool Changes
- Fewer setups mean less downtime and lower labor costs.
- Extended tool life due to optimized cutting angles.
5. Wide Industry Applications
- Aerospace: Turbine blades, structural components.
- Medical: Implants, surgical instruments.
- Automotive: Engine blocks, complex molds.
Limitations of 5-Axis CNC Machining
1. High Initial & Maintenance Costs
- More expensive than 3-axis and 4-axis machines.
- Requires specialized maintenance and calibration.
2. Complex Programming Requirements
- Advanced CAM software and skilled programmers are necessary.
- Longer setup times due to intricate toolpath planning.
3. Specialized Operator Training Needed
- Operators must be trained in 5-axis kinematics and advanced CNC controls.
4. Not Suitable for All Applications
- Vibration issues may arise with certain tool angles.
- 3-axis machining may still be preferable for simpler parts.
Why Choose HL Parts for Your 5-Axis CNC Machining Needs?
After reading this guide, you should now have a deep understanding of 5-axis CNC machining and its transformative impact on manufacturing. While the initial investment may be higher, the long-term benefits in precision, efficiency, and versatility make it a worthwhile choice for high-end machining applications.
At HL Parts, we are a leading CNC machining service provider in China, equipped with state-of-the-art 5-axis CNC machines and a team of highly skilled engineers. We offer:
✔ High-precision parts with tight tolerances
✔ Competitive pricing and fast lead times
✔ Custom manufacturing solutions tailored to your needs
Whether you need prototyping or full-scale production, HL Parts is your trusted partner for 5-axis CNC machining excellence.
Upload your design today for a quote or expert consultation!