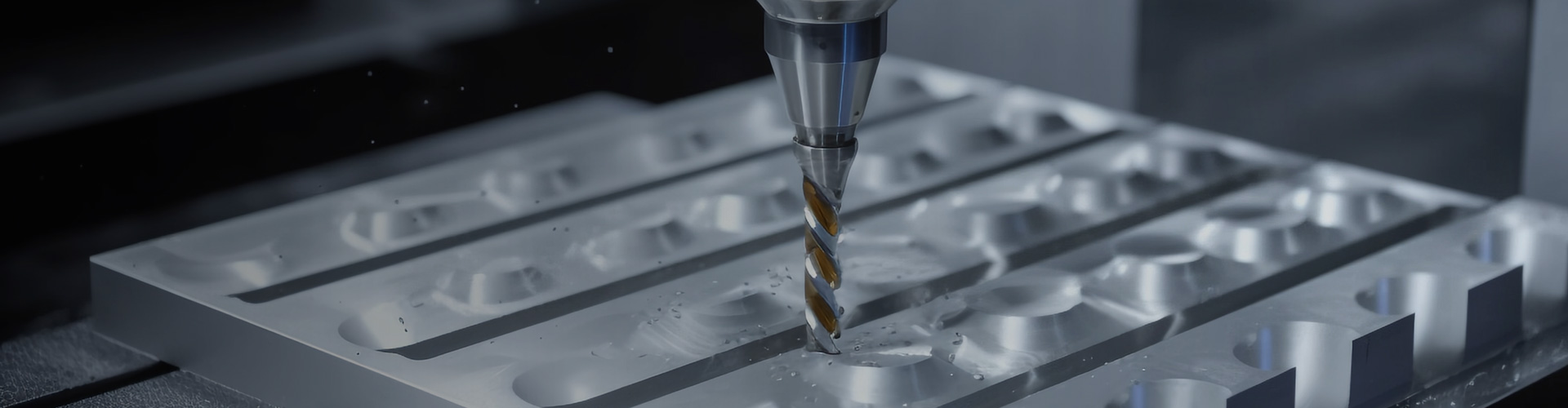
Manufacturing Process of High Pressure Check Valves
Comprehensive Analysis of High-Pressure Check Valves: Design, Applications, and Manufacturing
High-pressure check valves are critical components in fluid control systems, designed to prevent reverse flow and maintain system stability under extreme pressure conditions. These valves are extensively utilized in industries such as oil and gas, chemical processing, nuclear power, and hydraulic systems, where reliability under high-pressure environments is paramount.
Given the substantial fluid forces and dynamic pressure variations in high-pressure systems, the engineering of check valves must account for structural integrity, sealing efficiency, and resistance to cyclic fatigue. This analysis delves into the valve’s design principles, operational mechanisms, industrial applications, selection criteria, and manufacturing processes to provide a thorough understanding of their functionality and deployment.
1. Design and Operational Principles
(1) Fundamental Working Mechanism
High-pressure check valves operate autonomously, utilizing fluid dynamics to regulate flow direction. Under forward flow conditions, the valve disc opens, permitting unimpeded media passage. Conversely, reverse flow triggers rapid closure—either via spring force or backpressure—to prevent backflow.
In high-pressure systems, valve performance is challenged by significant pressure differentials, necessitating robust materials, optimized fluid dynamics, and enhanced sealing to mitigate energy losses and hydraulic shock.
(2) Key Structural Components
1. Valve Body:
- Constructed from high-strength, corrosion-resistant alloys (e.g., stainless steel, titanium, or nickel-based superalloys) to withstand extreme pressures and temperatures.
2. Sealing Mechanisms:
- Hard Seals: Metal-to-metal interfaces for high-temperature/pressure resilience.
- Soft Seals: Polymer or elastomer-based (e.g., PTFE) for superior leak-tightness in corrosive media.
3. Internal Assembly:
- Includes the disc, seat, spring, and flow-guiding chambers. Optimized geometries reduce turbulence and ensure swift, low-resistance actuation.
2. Types of High-Pressure Check Valves
- Piston Check Valves: Ideal for gas/liquid systems; feature stable actuation and high sealing reliability.
- Swing Check Valves: Suited for large-diameter pipelines; minimize flow resistance.
- Dual-Plate Check Valves: Mitigate water hammer effects in high-velocity systems.
3. Industrial Applications
(1) Oil & Gas Sector
- Pipeline Transport: Prevents backflow in crude oil/gas pipelines, ensuring pressure stability and safeguarding infrastructure.
- Wellhead Control: Maintains unidirectional flow of drilling fluids, critical for blowout prevention.
- Compressor Stations: Blocks reverse gas flow in compressors, enhancing operational safety.
(2) Hydraulic Systems
- Pump Protection: Secures hydraulic circuits from reverse flow, prolonging pump lifespan.
- Heavy Machinery: Used in CNC equipment, shipboard hydraulics, and lifting systems to ensure directional fluid control.
(3) High-Temperature Steam Systems
- Power Plants: Installed in boilers/steam lines to prevent steam reversal and optimize energy efficiency.
- Chemical/Pharmaceutical: Manages aggressive media in reactors and sterilization processes.
4. Selection Criteria
(1) Operational Parameters
- Pressure Rating: Valves must match system demands (e.g., ANSI 900–4500 class).
- Fluid Properties: Consider viscosity, temperature, and corrosiveness to select compatible materials.
(2) Material Considerations
- High-Temperature Alloys: Inconel or titanium for >500°C environments.
- Corrosion-Resistant Grades: Hastelloy or duplex stainless steels for acidic/alkaline media.
(3) Sealing Performance
- Zero-Leakage Designs: Critical for hazardous applications (e.g., nuclear).
- Abrasion-Resistant Coatings: Tungsten carbide or ceramic surfaces for erosive flows.
5. Manufacturing Processes
(1) Material Selection
- ASTM/ASME-compliant forgings or castings with stringent non-destructive testing (NDT).
(2) Critical Production Steps
1. Valve Body Machining: Precision CNC turning/grinding to achieve tight tolerances.
2. Seat Surface Treatment: Hardfacing (e.g., Stellite) or lapping for optimal seal integrity.
3. Component Assembly: Laser-aligned disc/seat pairing and spring calibration.
(3) Comparative Challenges
- Swing valves require meticulous hinge durability testing; piston valves demand exact bore finishes.
6. Conclusion
High-pressure check valves are engineered to deliver reliability in demanding systems. Through advanced materials, precision manufacturing, and tailored designs, these valves ensure safe, efficient flow control. Proper selection—guided by operational needs and fluid characteristics—is essential to maximize performance and service life in critical applications.