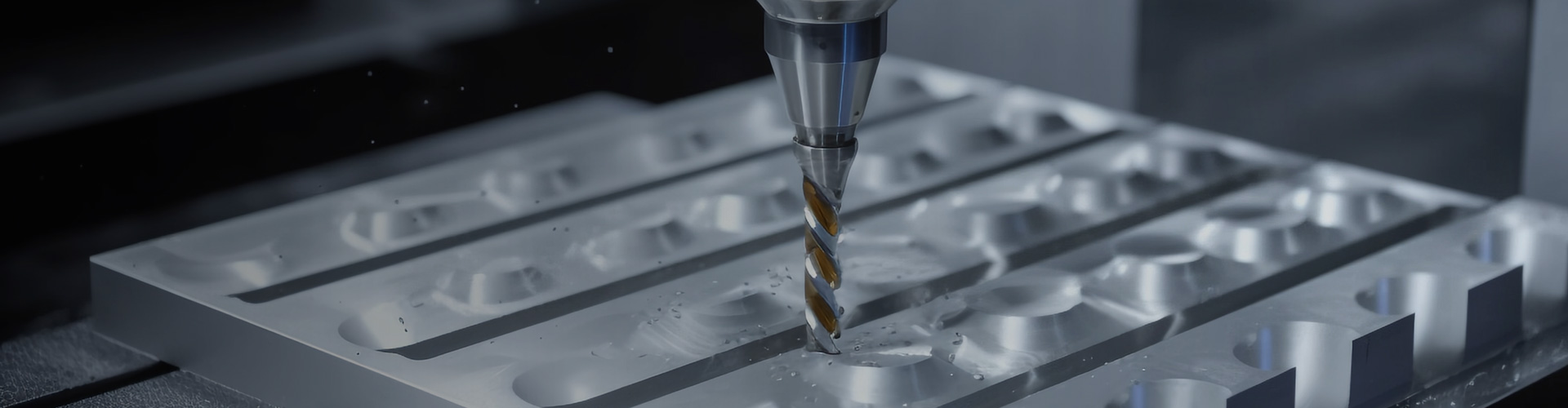
Fluid Control Valves: Operational Principles, Typology, and Industrial Applications
Fluid Control Valves: Operational Principles, Typology, and Industrial Applications
1. Introduction
Fluid control valves represent a critical class of industrial components designed to regulate fluid dynamics—including flow rate, pressure, and direction—across diverse sectors such as petrochemical processing, energy distribution, water treatment, and automated manufacturing. With advancements in materials science and Industry 4.0 technologies, modern fluid control valves now integrate enhanced durability, precision control, and intelligent functionalities to meet increasingly complex operational demands.
This technical analysis provides a systematic examination of valve architectures, operational mechanics, classification methodologies, and application-specific considerations, offering engineers and system designers a comprehensive reference for valve selection and deployment.
2. Structural Composition of Fluid Control Valves
(1) Valve Body
- Function: Serves as the primary pressure boundary and fluid conduit.
- Materials:
- Metallic: Carbon steel, stainless steel (SS316/SS304), duplex steels for corrosive/HPHT (High-Pressure High-Temperature) service.
- Non-Metallic: PTFE-lined bodies or engineered thermoplastics (e.g., PVDF) for chemical resistance in low-pressure systems.
(2) Closure Mechanism
- Disc/Ball/Plug: The movable element (e.g., ball in ball valves, disc in butterfly valves) that modulates flow by altering its positional relationship with the seat.
- Design Variants:
- Full Bore: Minimal flow restriction for high-Cv (Flow Coefficient) applications.
- Reduced Bore: Trade-off between flow capacity and compact sizing.
(3) Actuation Systems
- Manual: Handwheels/levers for infrequent operation in accessible locations.
- Automated:
- Pneumatic: Diaphragm/piston actuators for rapid response (e.g., quarter-turn valves).
- Electric: Motorized actuators for precise positioning (e.g., modulating control).
- Hydraulic: High-torque applications (e.g., large-diameter gate valves).
(4) Sealing Technologies
- Soft Seals: Elastomers (NBR, EPDM) or PTFE for bubble-tight shutoff in low-temperature services.
- Metal Seals: Inconel/Stellite overlays for abrasive or cryogenic fluids.
- Live-Loaded Packing: Spring-energized seals to maintain integrity under thermal cycling.
(5) Ancillary Components
- Stem Designs: Rising stem (visual position indication) vs. non-rising (space-constrained installations).
- Connections: Flanged (ASME B16.5/EN1092), threaded (NPT/BSP), or wafer-style for compact installations.
3. Operational Principles and Flow Dynamics
(1) Flow Regulation Mechanisms
- Throttling Control: Linear (globe valves) vs. equal percentage (characterized trim) flow characteristics for process optimization.
- Pressure Drop Management: Computational Fluid Dynamics (CFD)-optimized trims to minimize ΔP and cavitation risks.
(2) Pressure/Temperature Modulation
- Self-Regulating Valves: Pilot-operated designs (e.g., pressure reducing valves) maintain setpoints without external power.
- Thermostatic Blending Valves: Bimetallic elements modulate flow to achieve target temperatures.
(3) Actuation Dynamics
- Fail-Safe Modes: Spring-return (fail-close/fail-open) for safety-critical systems.
- Stroking Time: Critical for emergency shutdown (ESD) valves (e.g., API 6D requirements).
4. Valve Typology and Performance Characteristics
Valve Type | Operating Principle | Advantages | Limitations | Typical Applications |
Ball Vlave | 90° rotary motion of perforated ball | Low torque, bi-directional sealing | Limited throttling capability | Pipeline isolation, gas transmission |
Butterfly | Disc rotates perpendicular to flow | Compact, low-cost for large diameters | High ΔP at partial openings | HVAC, water distribution |
Globe | Linear stem motion lifts plug | Precise flow control, repairable | High head loss, bulky | Boiler feedwater, chemical dosing |
Gate | Parallel sliding disc | Full-bore, low friction loss | Slow operation, seat wear | Oil/gas pipelines (full-open/close) |
Diaphragm | Flexible membrane isolates fluid | Zero leakage, sterile design | Limited pressure/temperature range | Pharma, food processing |
5. Industrial Application Scenarios
(1) Oil & Gas Sector
- Upstream: Choke valves for wellhead pressure control (API 6A compliance).
- Midstream: Check valves in compressor stations to prevent backflow.
- Downstream: Cryogenic ball valves (-196°C) in LNG liquefaction plants.
(2) Power Generation
- Steam Turbines: HP bypass valves (ASTM A182 F91/F92 materials).
- Nuclear: Sealless valves (bellows-sealed) for primary coolant loops.
(3) Water/Wastewater
- Desalination: Titanium ball valves for seawater corrosion resistance.
- Sewage: Knife-gate valves for sludge handling.
(4) Specialty Industries
- Semiconductor: Ultra-high purity diaphragm valves with electropolished surfaces.
- Aerospace: Proportional flow control valves in fuel delivery systems.
6. Selection Methodology and Key Parameters
(1) Fluid Properties
- Corrosivity: Material selection per NACE MR0175 for sour service.
- Particulate Content: Erosion-resistant trim (e.g., tungsten carbide coatings).
(2) Operational Conditions
- Pressure Class: ASME 150–2500# or PN10–PN420 ratings.
- Temperature Range: Consider thermal expansion effects on seat materials.
(3) Performance Metrics
- Leakage Class: ANSI FCI 70-2 Class IV (metal seats) vs. Class VI (soft seats).
- Cv Value: Sizing calculations per ISA 75.01 standards.
(4) Automation Requirements
- Smart Valves: Embedded IoT sensors for predictive maintenance (PdM).
- SIL Rating: Safety Integrity Level compliance for process safety systems.
7. Intelligent Valve Technologies
(1) Digital Integration
- IIoT Connectivity: Modbus, PROFIBUS, or WirelessHART protocols for real-time monitoring.
- Edge Analytics: Vibration/temperature sensors detect cavitation or sticking.
(2) Advanced Control Algorithms
- Adaptive Tuning: PID loops auto-adjust based on process variability.
- Digital Twins: Virtual valve models simulate wear patterns.
8. Conclusion
Fluid control valves constitute a sophisticated intersection of mechanical engineering, materials science, and automation technologies. From traditional mechanical designs to AI-enabled smart valves, their evolution continues to address the challenges of efficiency, safety, and sustainability in modern industrial systems. A rigorous selection process—incorporating fluid dynamics, operational parameters, and lifecycle cost analysis—is essential to optimize valve performance across diverse applications. Future advancements will likely focus on nanotechnology-enhanced materials and quantum computing-optimized flow control algorithms.