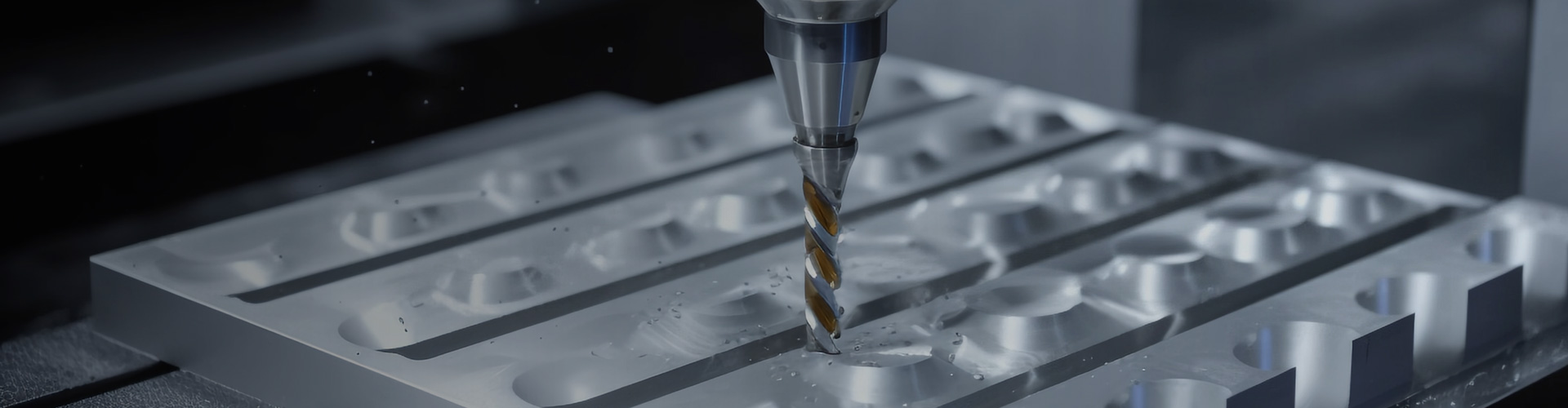
The Difference of the Manufacturing Processes
Most every product we use daily, from smartphones to cars, can trace its origins back to manufacturing processes. These processes not only determine the quality and production efficiency of products but also directly impact cost control and market competitiveness for businesses. In this article, we will define manufacturing processes, delving into their categories and various methods. Let’s get started now to explore their broad implications!
What Is Manufacturing Process?
To understand manufacturing processes, we must first examine the broader concept of manufacturing itself—the transformation of raw materials or components into finished products using tools, machinery, and human expertise.
Manufacturing traces its roots to prehistoric times, when early humans employed basic tools to cut, crush, and shape materials. As civilizations progressed, so too did manufacturing techniques, growing increasingly complex and refined. The Industrial Revolution was a pivotal moment, bringing steam power, mechanization, and mass production—fundamentally reshaping how goods were manufactured. In the modern era, manufacturing has evolved into a highly automated field, incorporating cutting-edge technologies like robotics, CNC machining, and additive manufacturing (3D printing).
A manufacturing process, more specifically, refers to the systematic procedures and operational sequences used to create a particular product. It encompasses critical phases such as design, material selection, fabrication, quality assurance, and final assembly—each playing an indispensable role in determining the functionality, durability, and success of the end product.
Five Categories of Manufacturing Processes
Manufacturing processes can be classified into five primary types based on production methods and output characteristics, each serving distinct industrial needs:
1. Custom Job Production
This approach caters to low-volume, high-mix manufacturing of specialized items. Tailored to specific customer requirements, it handles complex, one-off productions like industrial machinery or prototype development. While offering exceptional adaptability, the variable nature of operations makes production planning particularly challenging due to inconsistent workflows and specialized setups.
2. Unit-Based Assembly
Focused on creating identifiable end products from multiple components, this method assembles distinct items like vehicles, electronics, or furniture. Each product maintains traceability throughout creation, supporting significant customization potential. The automotive and consumer electronics sectors frequently employ this approach for its balance of standardization and configurability.
3. Mass Replication
Optimized for high-output production of identical goods, this system utilizes dedicated production lines with minimal variation. Automated systems dominate the process, ensuring rapid, consistent output with stringent quality protocols. Typical applications include automotive components, electronic microchips, and packaged consumables where uniformity is critical.
4. Group Production
Operating in cyclical production runs, this method processes materials in defined quantities before resetting for subsequent batches. Common in pharmaceuticals and specialty chemicals, it permits formulation adjustments between production cycles while maintaining equipment utilization. Strict cleaning and changeover procedures ensure batch integrity when switching product variants.
5. Uninterrupted Flow
Designed for perpetual operation with fluid inputs and outputs, this system processes bulk materials like petrochemicals or foodstuffs in continuous streams. Unlike batch or discrete methods, production occurs without interruption until planned maintenance, maximizing throughput for homogeneous outputs where product differentiation occurs through parameter adjustments rather than line reconfiguration.
What Are The Different Manufacturing Methods?
Each manufacturing category encompasses multiple specialized approaches designed to optimize production outcomes. Below, we examine seven fundamental manufacturing methodologies along with their specific variations.
1. Subtractive Manufacturing
Subtractive Manufacturing: Precision Through Material Removal
This fundamental manufacturing approach systematically removes material from solid blocks to achieve precise geometries across various materials like metals, polymers, ceramics, and engineered composites. Today's computer-controlled CNC systems have elevated these processes, delivering exceptional speed and micron-level accuracy for both complex contours and refined surface finishes. The technique is particularly valuable for job shops and discrete manufacturers producing specialized components.
Key Subtractive Techniques:
- Lathe Turning – Rotating workpieces are shaped by stationary cutting tools to produce axisymmetric components
- Precision Milling – Multi-axis cutting tools progressively carve complex 3D geometries from solid stock
- Hole Generation – Encompasses drilling (creating holes), boring (enlarging holes), and reaming (finishing holes) for dimensional accuracy
- Abrasive Machining – Includes grinding operations that achieve ultra-fine surface textures and tight tolerances
- Advanced Cutting Methods :
Laser systems for thermally precise cuts in delicate materials
EDM for intricate shapes in superhard conductive metals
Hydraulic abrasion cutting for heat-sensitive materials via ultrahigh-pressure water jets
This spectrum of material removal processes enables manufacturers to select the optimal balance of precision, surface quality, and production efficiency for each application.
2. Joining
Joining is the process of permanently or semi-permanently connecting two or more pieces of material to create an assembly. This technique is widely used in manufacturing complex products that is often impractical to produce directly. By producing multiple simpler components and then joining them, production costs for complex parts can be reduced. Additionally, joining processes allow for the replacement of faulty components without discarding the entire product. Some examples of joining processes are:
Welding: A process that fuses materials by applying heat, pressure, or both, together with the addition of a filler material to form a strong joint upon cooling.
Brazing: A joining method where a filler metal with a melting point higher than that of soldering but lower than the base materials is melted and flowed into the joint by capillary action.
Soldering: Similar to brazing, but performed at lower temperatures. A filler metal (solder) is melted and drawn into the joint between closely fitted parts.
Adhesive Bonding: A process where an adhesive material is applied between the surfaces to be joined, creating a bond upon curing.
Mechanical Assembly: Connecting components using fasteners such as bolts, nuts, rivets, or screws.
Interference Fit (Press Fit): A method where parts are joined by forcefully pressing them together, creating a tight fit due to the interference between the parts.
Others: Such as clinching and crimping, which are specialized joining techniques.
3. Forming
Forming Processes: Shaping Materials Through Deformation
Forming represents a fundamental manufacturing approach where materials - primarily metals - are reshaped through controlled mechanical forces without adding or removing material. This plastic deformation technique offers exceptional material efficiency while enhancing mechanical properties through work hardening and grain structure alignment.
Primary Forming Techniques:
- Forging
Utilizes compressive forces on heated metal to achieve superior strength characteristics
Methods include:
• Hammer forging (impact deformation)
• Press forging (gradual pressure application)
• Roll forging (continuous shaping)
- Sheet Metal Forming
- Stamping: High-speed pressing of sheet metal between precision dies
- Fine Blanking: Produces smooth-edged components in single operations
- Progressive Dies: Multi-stage forming for complex geometries
- Profile Shaping
- Press Brake Bending: Creates precise angles in sheet materials
- Roll Forming: Continuous bending for long, uniform sections
- Tube Bending: Specialized forming of hollow sections
- Bulk Deformation
- Flat Rolling: Reduces thickness while improving surface finish
- Shape Rolling: Produces structural sections (I-beams, rails)
- Ring Rolling: Creates seamless annular components
- Continuous Forming
- Direct Extrusion: Forces material through stationary dies
- Indirect Extrusion: Die moves relative to billet
- Hydrostatic Extrusion: Uses fluid pressure for brittle materials
These processes enable cost-effective production of high-strength components while maintaining material integrity and minimizing waste - making them indispensable for automotive, aerospace, and construction applications.
Key Advantages:
✓ Preserves material continuity
✓ Enhances mechanical properties
✓ Suitable for mass production
✓ Minimal material loss
4. Casting
Metal Casting: Shaping Molten Materials
The casting process transforms liquid metal into solid components by pouring it into prepared molds. After solidification, the mold is removed to reveal the final casting. This versatile manufacturing technique offers multiple approaches to suit different production needs:
Primary Casting Methods:
1. Sand Casting
- Utilizes bonded sand molds
- Economical for small batches and large parts
- Accommodates nearly all metal alloys
- Requires secondary finishing operations
2. Precision Investment Casting
- Employs sacrificial wax patterns
- Delivers exceptional detail replication
- Ideal for complex aerospace and medical components
- Higher per-unit costs justify superior quality
3. Rotational Casting
- Spins molds to distribute metal centrifugally
- Produces superior density in cylindrical forms
- Common for pipes, rings, and bushings
4. High-Pressure Die Casting
- Forces metal into steel dies under pressure
- Enables thin walls and fine details
- Dominates automotive and consumer goods production
- Limited to non-ferrous alloys
5. Reusable Mold Casting
- Uses permanent metal molds
- Offers better thermal control than sand casting
- Suitable for medium
5. Molding
Molding is similar to the casting process, but molding is more commonly associated with plastics, while casting mainly deals with metals. In molding, molten material is poured into a mold to solidify into the desired shape. Although creating molds is costly and time-consuming, the process is ideal for mass production of parts with precise dimensions and good surface finishes. The reusable nature of molds also reduces production costs. The common molding methods include:
Injection Molding: A highly versatile process for producing plastic parts. It involves injecting molten plastic into a closed mold cavity under high pressure. Once the plastic cools and solidifies, the mold is opened, and the part is ejected. This method offers high production rates, excellent repeatability, and the ability to produce complex shapes with fine details, making it a cost-effective solution for many industries.
Compression Molding: It involves placing a pre-measured amount of molding material into an open mold cavity. The mold is then closed, and pressure is applied to shape and cure the material. This method is suited for materials with low flow characteristics and is ideal for producing high-strength, high-density parts that are large, flat, or moderately curved.
Blow Molding: A process used to create hollow plastic parts by inflating a heated plastic tube (parison) until it fills the mold cavity. It is efficient for high-volume production of hollow plastic parts such as bottles, containers, and pipes, and is relatively low-cost.
Rotational Molding: A process used to create hollow plastic products of various sizes and shapes. It involves filling a heated mold with plastic resin and slowly rotating it around two perpendicular axes. The resin melts and coats the interior of the mold, forming a hollow part. This method has low tooling costs and the ability to produce large, complex parts with smooth interior surfaces, thick walls, and minimal assembly requirements. It is particularly suitable for low-volume production runs and custom designs.
Thermoforming (Hot-Air Forming or Vacuum Forming): A plastic forming process that utilizes heat and pressure to shape a plastic sheet into a desired three-dimensional form. This method offers low tooling costs, quick production cycles, and flexibility in design and material choices. It is commonly used for packaging, disposable cups, trays, lids, and other lightweight plastic products.
6. Additive Manufacturing
Additive Manufacturing: Layer-by-Layer Fabrication
Commonly referred to as 3D printing, additive manufacturing constructs objects through successive material deposition based on digital design files. This innovative approach enables unparalleled design freedom, minimal material waste, and the production of complex geometries that would be impossible with traditional methods. Suitable for both prototyping and end-use parts, AM works with various heat-fusible materials including engineering-grade plastics and high-performance metals.
Key Additive Manufacturing Technologies:
1. Powder Bed Fusion (SLS/SLM)
- Laser Sintering (SLS): Precisely fuses polymer powders using a laser beam, creating durable parts with mechanical properties close to injection-molded components
- Laser Melting (SLM): Fully liquefies metal powders to produce aerospace-grade components with exceptional structural integrity
2. Photopolymerization (DLP)
- Cures liquid resin rapidly using projected light patterns
- Delivers micron-level resolution for intricate designs
- Dominates applications requiring extreme precision
3. Material Extrusion (FDM/FFF)
- Deposits thermoplastic filaments through heated nozzles
- Most accessible and cost-effective 3D printing method
- Widely used for functional prototyping
4. Binder Jetting
- Bonds powder particles using liquid binding agents
- Enables full-color printing and large batch production
- Suitable for both metal and sand casting molds
5. Directed Energy Deposition
- Melts material simultaneously with deposition
- Ideal for large-scale metal part repair and hybrid manufacturing
Industry Applications:
- Aerospace: Lightweight structural components
- Medical: Patient-specific implants and surgical guides
- Automotive: Rapid prototyping and custom tooling
- Consumer Goods: Mass customization opportunities
This digital fabrication technology continues to evolve, enabling distributed manufacturing and on-demand production across global supply chains.
Surface Treatment Processes
Surface Engineering: Enhancing Material Performance
Various techniques modify material surfaces to improve:
- Durability (wear/corrosion resistance)
- Functionality (friction/adhesion properties)
- Aesthetics (finish/appearance)
Core Methods:
- Mechanical: Bead blasting, polishing
- Chemical: Conversion coatings, passivation
- Electrochemical: Anodizing, electroplating
- Deposition: Powder coating, PVD
Applied across aerospace, automotive, medical and consumer industries..
Three Types of Manufacturing Strategies
Manufacturing Strategies for Demand Fulfillment
1. Forecast-Driven Production (MTS)
- Produces inventory based on demand predictions
- Enables instant order fulfillment from stock
- Risks overproduction if forecasts are inaccurate
- Ideal for stable-demand, fast-moving goods
2. Demand-Triggered Production (MTO)
- Begins manufacturing upon confirmed orders
- Eliminates finished goods inventory
- Accommodates high customization
- Results in longer customer wait times
- Best for specialized/low-volume items
3. Modular Assembly Approach (MTA/ATO)
- Stocks pre-made components
- Final assembly occurs post-order
- Balances speed and customization
- Reduces inventory costs versus full MTS
- Common for configurable products
Each strategy presents distinct trade-offs between responsiveness, efficiency, and inventory risk, allowing manufacturers to align operations with market requirements..
Conclusion
Manufacturing Process Overview
The wide array of manufacturing techniques demonstrates how different methods serve distinct industry needs and production objectives. Each process offers unique advantages in efficiency, cost control, and quality assurance.
At HL Parts, we specialize in CNC machining and sheet metal fabrication, complemented by our 3D printing and injection molding capabilities. Our comprehensive services ensure tailored solutions for your production requirements.
For expert guidance, contact HL Parts today!