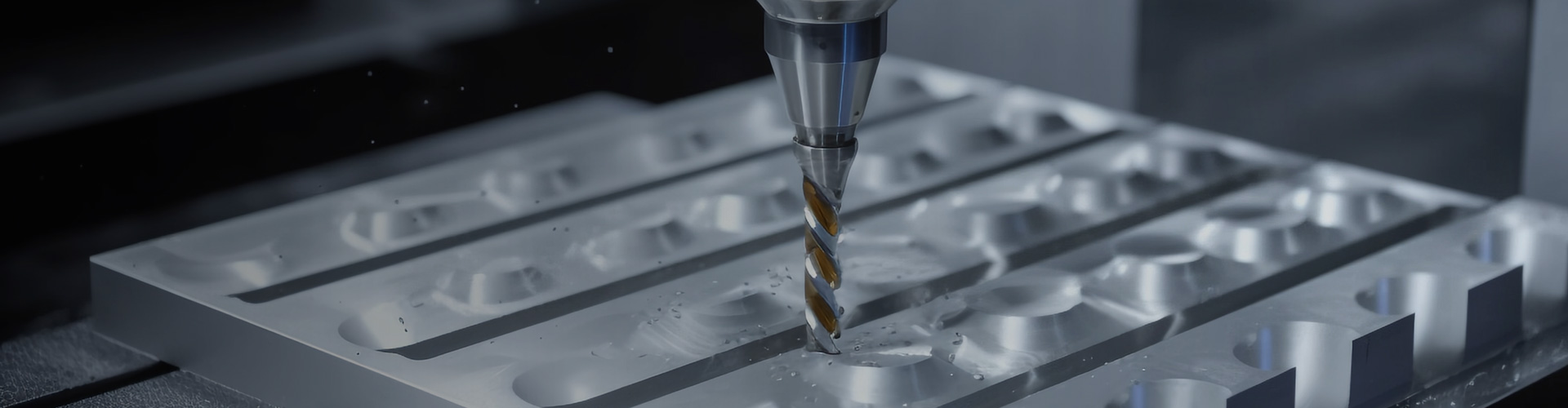
8 Plastic Fabrication Methods and Their Usages
Plastic fabrication plays a vital role in modern life, from everyday household items to specialized industrial parts. Manufacturers rely on various production techniques—such as injection molding, extrusion, —to create plastic components in diverse shapes and functions. But how do you determine the best method (or combination of methods) for your project? Key considerations include budget constraints, part complexity, material properties, and production scale. Below, we explore 8 widely used plastic fabrication techniques, detailing their working principles, advantages, drawbacks, and common use cases.
Injection Molding
Injection molding is a widely used plastic fabrication technique that involves melting plastic pellets (primarily thermoplastics, though some thermosets can also be used) and injecting the molten material into a precision mold under high pressure. The process relies on a reciprocating screw system to ensure consistent material flow. To enhance efficiency, modern molds feature built-in cooling channels that rapidly solidify the plastic, ensuring dimensional accuracy and fine detail reproduction. Once cooled, the mold opens, and the finished part is ejected.
Tooling & Durability
Injection molds are typically constructed from hardened steel to endure high pressures, temperatures, and prolonged mass production. For lower-volume runs, more affordable aluminum molds are an option, though they wear faster and have a shorter lifespan.
Design Considerations & Costs
While injection molding can produce highly intricate parts, complex geometries—such as deep undercuts, fine internal structures, or intricate details—increase mold complexity and cost. Following Design for Manufacturing (DFM) principles helps optimize part design and reduce expenses.
Initial mold fabrication can take several months and cost anywhere from thousands to hundreds of thousands of dollars. However, once operational, injection molding offers extremely fast cycle times, making it ideal for high-volume production with low per-unit costs compared to other methods.
Common Applications
- Consumer Goods: Toys, food containers, electronic housings.
- Automotive Components: Dashboards, bumpers, interior trim.
- Medical Devices: Syringes, surgical tool casings, IV components.
This method excels in mass production, delivering high precision, repeatability, and cost efficiency at scale.
Compression Molding
Compression molding is a manufacturing technique primarily used for thermosetting polymers (e.g., phenolics, epoxies) and elastomers (e.g., silicone rubber). The process involves:
1. Preheating the raw material (usually in pellet or preform shape).
2. Placing it into an open mold cavity.
3. Closing the mold with a hydraulic press, applying heat and pressure to shape and cure the material.
Unlike injection molding, compression molding does not require complex gates, runners, or overflow systems, leading to higher material efficiency and reduced waste.
Advantages & Limitations
✔ Lower tooling costs – Simpler mold structure makes it ideal for low-to-medium production runs.
✔ Suitable for large parts – Commonly used for automotive panels and composite components.
✔ Superior material properties – Thermosets cure irreversibly, offering high heat resistance and structural strength.
✖ Slower cycle times – Curing takes longer than injection molding cooling phases.
✖ Flash control challenges – Excess material (flash) may escape, requiring secondary trimming.
✖ Less precision – Tight tolerances are harder to achieve compared to injection molding.
Typical Applications
- Rubber Products: Gaskets, O-rings, keypads.
- Automotive Parts: Hoods, fenders, spoilers, brake pads.
- Electrical Insulators: Circuit breakers, high-voltage components.
- Composite Manufacturing: Fiberglass-reinforced plastics (FRP).
Compression molding is a cost-efficient choice for durable, heat-resistant parts where high-volume production isn’t required.
Blow Molding
Blow molding creates thin-walled, hollow plastic components by inflating a heated plastic tube (parison) or preform with compressed air. The softened thermoplastic expands to conform to the mold cavity, cools, and is ejected as a finished part.
Key advantages:
✔ High-speed production – Fully automated for mass manufacturing.
✔ Low per-unit costs – Ideal for high-volume orders.
✔ Lower pressure requirements – Reduces tooling expenses vs. injection molding.
Types of Blow Molding
1. Extrusion Blow Molding (EBM)
- Process: A continuous parison is extruded, clamped into a mold, and inflated.
- Pros: Handles large, complex shapes (e.g., fuel tanks, industrial drums); versatile material compatibility.
- Cons: Variable wall thickness; excess flash requires trimming (higher waste).
2. Injection Blow Molding (IBM)
- Process: A preform is injection-molded, reheated, and blown into shape.
- Pros: Superior precision, uniform walls, and smooth finishes; minimal waste.
- Cons: Limited to smaller parts (e.g., bottles); less efficient for large containers.
3. Injection Stretch Blow Molding (ISBM)
- Process: Preforms are stretched longitudinally before blowing to align polymer chains.
- Pros: Enhances strength, clarity, and barrier properties (e.g., PET bottles).
- Cons: More complex/expensive; best for PET, PP, and similar resins.
Typical Applications
- Packaging: Beverage bottles, shampoo/detergent containers.
- Automotive: Fuel tanks, air ducts, coolant reservoirs.
- Industrial/Medical: Chemical storage, sterile fluid containers.
Blow molding excels in producing lightweight, durable hollow parts at scale, with method selection depending on part size, material, and performance needs.
Rotational Molding
Rotational molding is a specialized manufacturing method for creating hollow, seamless plastic components with uniform wall thickness. Unlike blow molding, rotomolding uses low-pressure centrifugal force rather than compressed air to shape parts.
How It Works:
1. Material Loading: Plastic powder or liquid resin is placed into a hollow mold.
2. Heating & Rotation: The mold is heated while rotating biaxially (or multi-axially), evenly distributing the molten plastic.
3. Cooling & Demolding: The mold is slowly cooled, then opened to release the finished part.
Key Advantages
✔ Low-Cost Tooling – Molds (often aluminum or epoxy) are cheaper than high-pressure alternatives.
✔ Design Flexibility – Allows embedded inserts (metal fittings, reinforcements) and complex geometries.
✔ Uniform Wall Thickness – Ideal for large, stress-resistant components.
Limitations
✖ Slower Cycle Times – Heating/cooling phases make it less efficient for mass production.
✖ Looser Tolerances – Not suitable for high-precision applications.
Ideal Applications
- Industrial Storage: Water tanks, chemical containers, fuel tanks.
- Recreational Equipment: Kayaks, playground structures, outdoor furniture.
- Heavy-Duty Containers: Bulk storage bins, agricultural equipment.
Rotomolding is a cost-effective solution for low-to-medium production runs of large, durable hollow parts, offering superior durability and design versatility compared to blow molding for certain applications.
Vacuum Casting
Vacuum casting (urethane casting) is a soft tooling technique that uses silicone molds to produce high-quality plastic or elastomer parts. It bridges the gap between prototyping and small-batch production, offering fast turnaround and cost efficiency compared to hard tooling methods like injection molding.
Key Steps:
1. Master Model Creation: A precision pattern is made via CNC machining or 3D printing.
2. Silicone Mold Fabrication: The master is encased in liquid silicone and oven-cured (8–16 hours at 40°C).
3. Vacuum Casting: Liquid polyurethane resin is poured into the mold under vacuum to eliminate bubbles, then oven-cured.
4. Demolding: The silicone mold is split to extract the final part.
Advantages
✔ Rapid & Economical – Silicone molds are 10x faster/cheaper than metal tooling.
✔ High Fidelity – Replicates fine details (even textures/undercuts) from the master model.
✔ Material Versatility – Supports colored, transparent, or filled resins (e.g., flame-retardant, rubber-like).
Limitations
✖ Limited Mold Life – Silicone molds degrade after 20–30 casts, restricting volume.
✖ Thermal Constraints – Unsuitable for high-temp thermoplastics or heavy-load applications.
✖ Master-Dependent – Part quality hinges on the precision of the initial model.
Typical Applications
- Prototyping: Functional testing, design validation.
- Low-Volume Production: Niche-market parts, pre-series batches.
- Aesthetic/Functional Parts: Consumer electronics casings, medical device housings.
Vacuum casting excels in delivering injection-molding-quality parts for short runs, making it ideal for product development and market testing.
Plastic CNC Machining
CNC machining transforms solid plastic stock into precision parts through computer-controlled subtractive processes including milling, turning, and drilling. This method supports diverse engineering plastics (ABS, Nylon, PE, PP) and excels where molding processes reach their limitations.
Key Characteristics:
- Geometric Freedom: Capable of producing deep cavities, undercuts, and multi-axis features
- Exceptional Precision: Achieves tight tolerances (±0.127mm) and superior surface finishes
- Material Efficiency: Works with stock shapes (sheets, rods, blocks) without mold constraints
Technical Advantages
✔ Rapid Implementation: No tooling required - direct from CAD to production
✔ Design Flexibility: Accommodates late-stage modifications effortlessly
✔ Material Integrity: Preserves original plastic properties (no thermal degradation)
✔ Prototype-to-Production: Seamlessly scales from single pieces to medium batches
Economic & Technical Considerations
◉ Cost Drivers:
- Complex geometries increase machining time
- Multi-axis operations require specialized setups
- Internal features may need EDM or specialty tooling
◉ Process Limitations:
- Higher material waste compared to molding
- Challenging for organic/internal contours
- Labor costs dominate at higher volumes
Industry Applications
Aerospace:
- Lightweight structural components
- Avionics enclosures
- Custom mounting solutions
Medical Technology:
- Sterilizable instrument housings
- Diagnostic equipment parts
- Surgical tool components
Industrial Equipment:
- Wear-resistant gears
- Custom sealing solutions
- Machinery interface parts
This subtractive method provides unmatched precision for demanding applications where material properties and dimensional accuracy are critical, particularly in low-to-medium volume scenarios.
Plastic Extrusion
Plastic extrusion transforms raw thermoplastic pellets into continuous linear products through a precisely controlled thermal-mechanical process:
1. Material Preparation - Virgin or compounded pellets are fed into the hopper
2. Plasticization Phase - A rotating screw conveys material through heated zones (120-300°C)
3. Homogenization - Mixing elements create uniform melt viscosity
4. Die Formation - Molten polymer is shaped through precision tooling
5. Cooling & Sizing - Calibration systems establish final dimensions
6. Haul-off & Cutting - Pullers maintain tension while cutters create discrete lengths
Technical Advantages:
▸ High Throughput - Continuous operation yields kilometers of product daily
▸ Material Efficiency - Near 100% material utilization with regrind capability
▸ Profile Consistency - Maintains ±0.1mm dimensional stability
▸ Surface Quality - Achieves Ra <0.8μm without secondary finishing
Specialized Variants:
- Co-extrusion: Multilayer structures for barrier properties
- Tandem Systems: In-line orientation for enhanced strength
- Micro-extrusion: Sub-millimeter precision profiles
Design Constraints:
◈ Limited to constant cross-sections
◈ Minimum wall thickness ≥0.3mm
◈ Corner radii >0.5mm required
◈ Draft angles necessary for complex dies
Industrial Applications:
Construction Sector
- Structural profiles (window/door systems)
- Weatherproof membranes
- Piping systems (PVC, PP, PE-Xa)
Packaging Industry
- Flexible packaging films
- Thermoformable sheets
- Protective edge trims
Electrical Engineering
- Wire insulation (up to 35kV)
- Cable conduits
- Busbar sheathing
Consumer Goods
- Decorative trim
- Footwear components
- Furniture edge banding
This continuous forming process remains unmatched for high-volume production of thermoplastic profiles, combining efficiency with consistent quality across kilometers of output. Modern extrusion lines incorporate advanced process control (APC) systems and real-time monitoring for optimal production stability.
Plastic Pultrusion
Pultrusion is a continuous, automated process for manufacturing fiber-reinforced polymer (FRP) profiles with exceptional mechanical properties:
1. Fiber Feeding - Continuous rovings of glass/carbon/aramid fibers are aligned and tensioned
2. Resin Impregnation - Fibers are drawn through a resin bath (typically polyester, vinylester, or epoxy)
3. Preforming - Excess resin is removed and fibers are pre-shaped
4. Curing - The assembly passes through a heated die (120-180°C) for thermosetting
5. Pulling & Cutting - Hardened profile is continuously pulled and cut to length
Key Advantages
▸ Superior Strength-to-Weight Ratio - Exceeds steel in specific strength
▸ Corrosion Resistance - Ideal for harsh chemical/environmental conditions
▸ Dimensional Stability - Maintains ±0.5mm tolerance over 100m lengths
▸ Continuous Production - Enables unlimited length capability
Material Combinations
- Glass fiber + polyester (most economical)
- Carbon fiber + epoxy (aerospace grade)
- Hybrid fiber systems (custom performance)
Technical Specifications
◈ Standard profile width: 10mm-1m
◈ Minimum thickness: 1.5mm
◈ Fiber content: 40-70% by volume
◈ Production speed: 0.5-2m/min
Industry Applications
- Civil Infrastructure
- Bridge decking systems
- Pier reinforcement beams
- Utility pole crossarms
Industrial Platforms
- Chemical-resistant walkways
- Electrically insulating structures
- High-load cable trays
Specialty Equipment
- Lightweight tower structures
- Electromagnetic transparent supports
- High-voltage insulators
This process uniquely combines the efficiency of continuous production with the performance of advanced composites, making it indispensable for structural applications where corrosion resistance and durability outweigh initial material costs. Modern developments include UV-resistant formulations and fire-retardant systems for demanding environments.
Conclusion
Final Thoughts: Selecting the Right Plastic Fabrication Approach
This guide has equipped you with essential knowledge about different plastic manufacturing processes and their unique advantages. Making the right fabrication choice is crucial for achieving:
✔ Optimal production efficiency
✔ Consistent product quality
✔ Cost-effective manufacturing
Why Partner with HL Parts?
As specialists in plastic fabrication, we offer:
- Comprehensive solutions from prototyping to full-scale production
- Expert guidance on design optimization and material selection
- Precision manufacturing across all volume requirements
Let's collaborate to transform your concepts into high-quality plastic components. Contact our team today to discuss your project requirements and discover how we can add value to your production process.