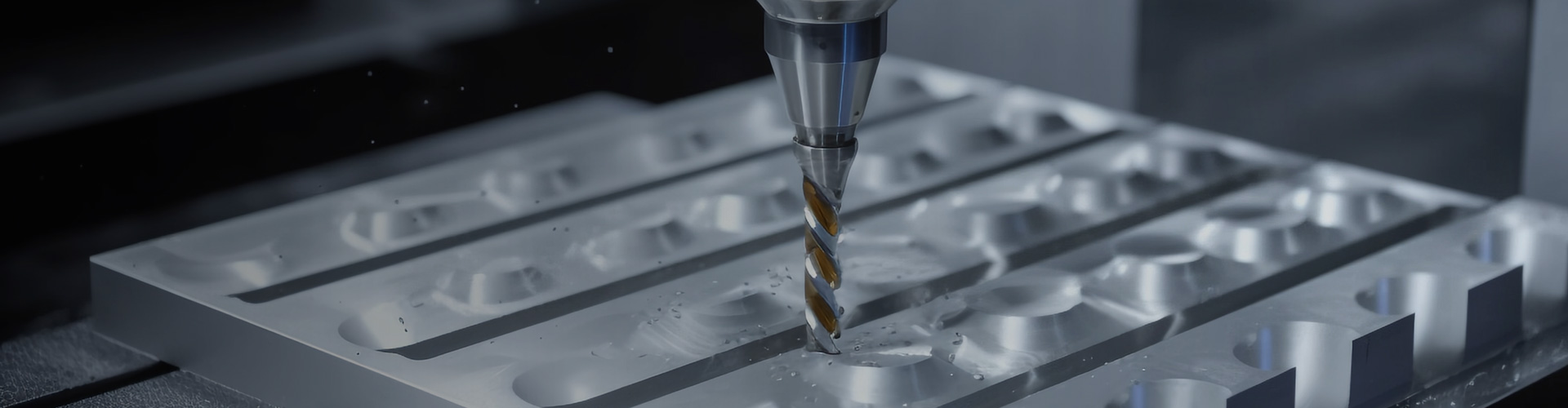
Understanding the Springs' Uses and Materials
Springs, essential mechanical components, are engineered to store and release energy when compressed, stretched, or twisted. Constructed from materials such as steels or specialized alloys, they are manufactured through processes like winding, heat treatment, grinding, coating, and finishing. In machinery, springs serve functions like shock absorption, vibration damping, and controlled motion. They also enhance daily life, improving vehicle ride quality, enabling accurate timekeeping, and providing comfort in furniture. Springs can be custom-made for specific needs or mass-produced for general use. Understanding their workings, types, applications, and selection criteria is crucial for any project.
How Springs Work
Springs deform under applied force, storing energy in the process. This deformation generates a restorative force that returns the spring to its original shape once the external force is removed, as described by Hooke's Law. Formulated by Robert Hooke in the 17th century, this law states that the force (\(F\)) applied to a spring is proportional to its displacement (\(x\)) from the equilibrium position, expressed as \(F = -kx\). The negative sign indicates that the restoring force acts in the opposite direction of the displacement. The spring constant (\(k\)) measures the spring's stiffness and varies based on factors like wire diameter, coil diameter, number of coils (for linear springs), torsion angle, and arm length (for torsion springs).
Types of Springs and Their Applications
Springs are categorized into three main types: mechanical, gas, and air springs. Gas springs, using compressed sealed gas, are common in automotive tailgates and adjustable chair backs. Air springs, which rely on compressed air, are used in vehicle suspension systems. This article focuses on mechanical springs, the most prevalent type in consumer devices and industrial equipment, further divided into helical, disc, and leaf springs.
Helical Springs
Helical springs, or coil springs, are formed by winding wire into a helical shape using spring coiling machines. Their elasticity and flexibility allow them to absorb shock and maintain force across various loads.
Compression Springs: These open-coiled springs with constant coil diameter and spacing can only be compressed axially. Precision grinding at the ends ensures even force distribution and stable assembly. They are used in mattresses, valves, ball-point pens, and weighing machines.
Extension Springs: Tightly coiled, they resist stretching forces. Ends are often formed into loops or hooks for attachment. CNC machining creates complex end shapes for custom springs. They are found in garage doors, weighing machines, and automotive suspensions.
Torsion Springs: With ends fixed to other components, they generate torque when those components rotate around the spring's center. They are used in hinges, counterbalances, door closers, and garage doors. Spiral springs, a type of torsion spring, are made from coiled rectangular metal strips and are ideal for mechanical watches, toys, and seat recliners due to their constant energy release.
Disc Springs
Disc springs are made from flat metal sheets via high-precision stamping. Their conical shape allows for stacking to achieve specific force-deflection characteristics, making them suitable for high-force, limited-space applications.
Belleville Springs: With a standard conical design, thicker at the edges and thinner at the center, they have high spring rates and load capacities. They are used in mechanical tools, valves, clutches, and circuit breakers.
Curved Disk Springs: Also known as crescent washers, their curvature results in a predetermined deformation path under load. They are used in safety and pressure control valves for their non-linear load characteristics.
Slotted Disk Springs: Slots on the outer or inner diameter allow for lateral expansion during compression, reducing stiffness. Their non-linear load response makes them ideal for applications requiring precise force and displacement control, such as automatic transmissions and overload couplers.
Wave Disk Springs: Their undulating shape enables high axial compression in a compact space, offering a progressive load. They are used in valve assemblies, electronic devices, and lightweight machinery.
Leaf Springs
Leaf springs consist of layered, narrow plates, manufactured by cutting and shaping through hot or cold forming. Known for their strength and heavy-load capacity, they were once common in vehicle suspensions but are being replaced in some applications.
Mono-leaf Springs: Made from a single, tapered piece of metal, they are lighter yet capable of handling significant loads. They are popular in performance and light commercial vehicles.
Multi-leaf Springs: Comprising multiple stacked metal leaves of varying lengths, they distribute loads evenly, providing better shock absorption and durability. They are used in heavier vehicles like trucks, vans, and SUVs.
Materials for Springs
Springs are mainly made from metals, though composites and rubber are sometimes used. Common metal materials include:
High Carbon Steel: With a high carbon content (0.6 - 1.5%), it offers high hardness, strength, fatigue, and wear resistance but is brittle and prone to corrosion.
Low-Alloy Steel: Containing less than 5% alloying elements like nickel, chromium, and molybdenum, it enhances strength and toughness, has better corrosion resistance than carbon steel, and is cost-effective.
Stainless Steel: A high-alloy steel with at least 10.5% chromium, it's suitable for harsh environments. Additional elements improve strength, wear, and fatigue resistance, and it performs well in various temperatures.
Nickel Alloys: They offer excellent high-temperature and corrosion resistance with good mechanical strength, ideal for extreme conditions.
Copper Alloys: Known for their electrical and thermal conductivity, corrosion resistance, and ease of shaping, they are used in applications requiring conductivity, like battery contacts.
Titanium: Valued for its low density, high strength, and biocompatibility, it's used in medical devices, high-performance sports equipment, and aerospace components.
These materials often undergo treatments: cold drawing improves tensile strength; heat treatments like quenching, tempering, oil quenching, and bainite hardening enhance properties; surface treatments prevent oxidation; and stress relief removes internal stresses.
Benefits of Springs
Springs offer numerous benefits:
Vibration Damping: They reduce vibration intensity in systems, prolonging equipment life, improving operator comfort, and ensuring precise machinery operation.
Shock Absorption: Springs mitigate sudden impacts, providing a smoother ride in vehicles by absorbing road bumps.
Force Provision and Motion Control: They generate forces to control motion or maintain balance, like in door closers.
Support and Compensation: Springs support and adjust to different loads, providing comfort in office chairs.
Energy Storage and Release: They store energy during deformation and release it when needed, functioning like batteries in mechanical watches and toys.
Selecting the Right Spring
Choosing the appropriate spring is vital:
Select the Spring Type: Compression springs are for pushing motions, extension springs for pulling, and torsion springs for rotational movements. Each type has typical applications based on its properties.
Consider Application Requirements: Determine force requirements, including load type, maximum force, and safety factor, and translate them into spring design parameters. Evaluate environmental conditions, choosing materials like nickel alloys for high temperatures, titanium or stainless steel for corrosion, and high-strength materials for heavy loads. Also, consider space limitations, as different spring types suit different spatial constraints.
Stock vs. Custom: Stock springs are readily available and cheaper, while custom springs offer a precise fit. Choose a reliable manufacturer for custom springs, like Chiggo, which has over a decade of machining expertise.
Springs are indispensable in manufacturing. For high-quality custom springs, Chiggo is a trusted partner. Contact us today for more information.
Work with HL Parts for Custom Springs
Springs play a pivotal role in the manufacturing sector. If you are seeking a reliable partner to produce essential springs for your products, HL Parts is your ideal choice! With over a decade of machining expertise, our daily engagement with diverse springs provides us with unparalleled knowledge of their properties.
We are committed to helping you achieve your goals by delivering top-notch springs at a price that fits your budget. Contact us today for more information.