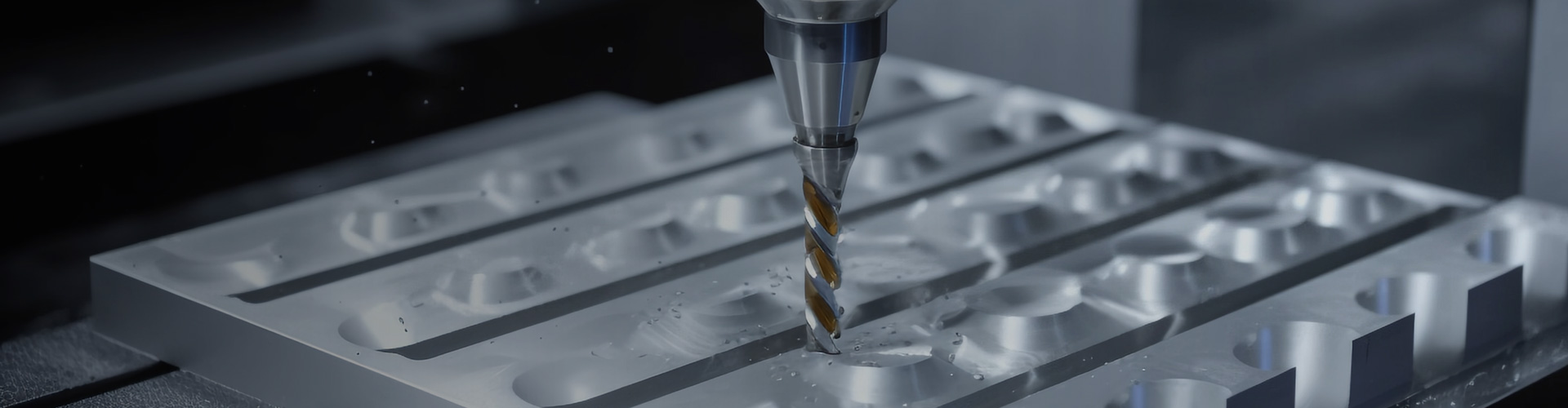
The Guidance of the Snap Fit Joints
Understanding Snap Fit Joints
Snap fit joints are a type of mechanical fastening mechanism that relies on interlocking features to connect two or more components. The term "snap fit" describes the process where a flexible element, such as a hook, bead, or protrusion, on one part engages with a corresponding receiving feature (like a groove or hole) on another part. This connection is achieved through the elastic deformation of the flexible element, which returns to its original shape once aligned with the mating part, creating a secure link.
These joints are designed to join parts without the need for additional fasteners like screws or adhesives. Plastics are the preferred material for snap - fit components due to their flexibility, which allows them to withstand repeated deformation during the snapping process without damage. Depending on the undercut design and assembly method, snap fit joints can be either permanent or detachable. They offer significant advantages in terms of time and cost savings, as they reduce material usage and eliminate the need for specialized tools. Their ease of assembly, often just a simple press or push, makes them ideal for automated production lines. Injection molding has long been a popular mass - production method for snap fit joints, while 3D printing has introduced new opportunities for rapid design testing and functional verification.
Types of Snap Fit Joints
Cantilever Snap Fit Joints
Cantilever snap fit joints are the most prevalent type. They feature a cantilever beam structure, fixed at one end and free - moving at the other. The beam can have various shapes, such as straight, L - shaped, and usually has a protrusion at the free end to interlock with a groove or hole on the mating part. During assembly, the beam bends to fit the other part and then springs back, securing the connection. This elastic deformation enables quick assembly, and in some cases, disassembly.
Benefits: They are relatively simple to design and manufacture, especially via injection molding. Their high flexibility allows for a wide range of deformation during assembly without damage, making them suitable for both permanent and detachable connections.
Limitations: Stress concentration often occurs at the base of the beam, which can lead to material fatigue, especially under heavy loads or frequent use.
Applications: Widely used in plastic enclosures of consumer electronics, battery covers of electronic devices, snap - on caps and lids for packaging, automotive interior components like dashboard panels, toy assemblies, and other lightweight components that require simple and secure connections.
U - shaped and L - shaped snap joints are variations of cantilever snap fits. U - shaped snap joints can have longer beams in compact spaces, reducing assembly forces and stress concentration. L - shaped snap joints provide directional locking and enhanced rigidity, suitable for side - assembly or applications where parts need to resist specific forces. These designs simplify the injection molding process by reducing the need for complex mold components.
Torsion Snap Fit Joints
Torsion snap fit joints differ from cantilever ones in that they rely on the twisting (torsional deformation) of a bar or shaft instead of linear bending. When an assembly force is applied, a torsional arm or lever rotates around a pivot point, allowing the locking feature to engage with the mating part. After engagement, the torsional arm returns to its original position due to the material's elastic torsion, securing the joint. This design enables quick assembly and, if designed for reversibility, easy disassembly.
Benefits: Ideal for designs with limited linear space, as they use a twisting motion. The stress is more evenly distributed compared to cantilever designs, reducing the risk of material fatigue.
Limitations: They are mainly suitable for rotational connections, which limits their application. The design is more complex, as the torsional element needs to balance flexibility and strength precisely. Repeated twisting can cause wear over time.
Applications: Commonly found in hinged covers and doors (e.g., glove boxes, access panels), latch mechanisms (such as suitcase locks), foldable devices (like flip phones), and interactive toys with rotating parts.
Annular Snap Fit Joints
Annular snap fit joints have a ring - like protrusion that snaps into a corresponding groove on the mating part, creating a 360° engagement around a cylindrical component.
Benefits: The even engagement around the circumference provides uniform stress distribution, enhancing joint strength and offering better sealing capabilities and high retention force.
Limitations: They have less flexibility during assembly compared to cantilever snap fits, as the ring - shaped protrusion must deform uniformly, which can be difficult for harder materials. They are often hard to disassemble once engaged, making them more suitable for permanent connections. The manufacturing process is more complex due to the need for precise molds and tight tolerances.
Applications: Used in bottle closures, plumbing connectors, medical device closures (where fluid or gas - tight seals are necessary), pen caps, marker lids, and automotive cylindrical parts (such as hose connectors, filters, and fluid reservoirs).
Designing Snap Fit Joints
Design Calculations
Design calculations for snap fit joints are vital for determining allowable deflection, strain limits, and mating forces. Conducting these calculations early in the design process allows for adjustments to dimensions, materials, and geometry, ensuring optimal performance before prototyping or production.
Cantilever Snap Joints
Key Parameters and Formulas:
Design Considerations:
Incorporate smooth transitions and fillets to reduce stress concentrations.
Keep deflection and strain within allowable limits to prevent material fatigue or failure.
Select materials with appropriate modulus of elasticity and strain capacity.
Torsion Snap Joints
Key Parameters and Formulas:
Design Considerations:
Choose materials with high shear strength and good torsional elasticity.
Optimize the length and radius of the torsion bar to manage deflection force and prevent over - stressing.
Include a return angle for separable joints.
Annular Snap Joints
Key Parameters and Formulas:
Design Considerations:
Design for multiaxial stress distribution.
Adjust the undercut based on material strain capacity and joint flexibility.
Use materials that can handle large deformations without permanent damage.
Common Design Problems and Solutions
Even with calculations, snap fit designs can face common issues that may lead to failure.
Common Issues
Stress Concentration: Occurs at sharp corners or abrupt transitions in the snap feature, potentially causing cracking or material failure over time.
Creep: A long - term deformation of materials (such as thermoplastics) under continuous load, which can loosen the joint.
Fatigue: Deterioration of a material due to cyclic loading, leading to crack formation and reducing joint reliability.
Tolerance Issues: Inaccurate manufacturing tolerances can result in misaligned snap features, causing poor connections or assembly difficulties.
Best Practices
Set Appropriate Tolerance: Balance the fit to avoid excessive stress during assembly or weak connections. Consider material shrinkage, temperature changes, and wear over time.
Add Fillets at the Base of the Cantilever: Reduce stress concentrations by adding rounded fillets. Limit the root thickness and ensure the radius meets a minimum requirement.
Taper the Snap Fit Design: Make the cross - section of the cantilever beam gradually smaller along its length to evenly distribute stress.
Increase the Width of the Clip (or Hook): Distribute the load over a larger area, reducing the risk of material fatigue, while maintaining an optimal balance of flexibility and strength.
Consider Adding Lugs: Guide components during assembly, improve alignment, and enhance the overall strength of the connection.
Partner with HL Parts
Snap fit joints are highly valued in various industries for their assembly simplicity, reusability, and cost - effectiveness. A well - designed snap fit joint can enhance product strength and user experience.
HL Parts is a trusted manufacturer of high - quality plastic and metal snap fit joints, with nearly 20 years of experience serving multiple industries. We offer custom manufacturing services, including CNC machining, injection molding, and 3D printing. Our experienced engineers can help you improve product performance and reduce costs. Submit your design file today and start your next project with us.