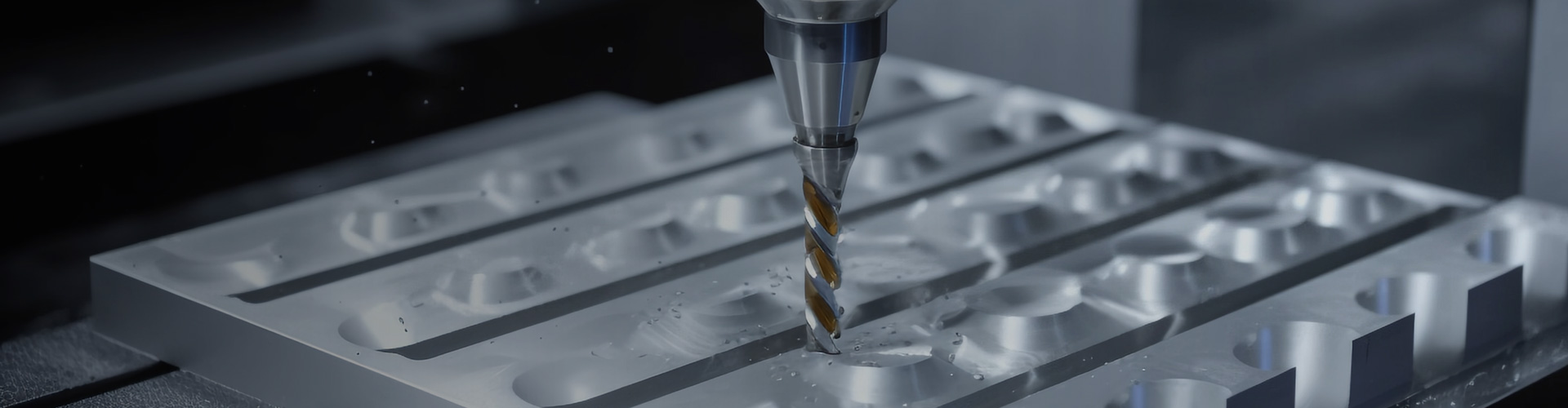
The Difference between Chamfers and Fillets
In our everyday surroundings, chamfered and filleted designs are omnipresent. From household appliances to furniture and children's toys, these design elements grace the edges of countless objects. They serve a vital purpose: safeguarding us from scratches and injuries. Similarly, consumer electronics leverage chamfers and fillets to not only enhance their visual allure but also elevate the tactile experience. In the realm of manufacturing, both processes play crucial roles in modifying product edges, driven by considerations of safety, aesthetics, and functionality.
Chamfers: The Sloped Edge Solution
A chamfer is characterized by a sloped or beveled edge on a component. Typically, it's cut at a 45 - degree angle, though other angles can be specified. This design eradicates sharp corners, creating a flat, angled surface where two surfaces intersect. Consider a bolt; the beveled edge at its tip is a chamfer. This angled cut not only gives the bolt a sleek appearance but also makes it safer to handle by eliminating hazardous sharp corners. Moreover, chamfers reduce stress concentrations, preventing cracks or breaks under load. They act as guides, facilitating the smooth insertion of bolts into nuts or threaded holes, streamlining the assembly process.
Chamfers can be crafted manually with hand tools. However, for greater precision, automated processes like CNC machining, laser cutting, or grinding are employed. In mechanical assembly, they guide components such as bolts, screws, pins, and gears. They also function as insertion guides for circuit boards, slots, and connectors. In welding, especially for V - shaped joints or when deeper welds are required, chamfering provides additional space for welding material, resulting in stronger, more structurally sound joints.
Fillets: The Rounded Transition
A fillet, on the other hand, introduces a smooth, rounded transition between two intersecting surfaces. On internal corners, it forms a concave curve, while on external corners, it creates a convex curve. Modern furniture often showcases fillets, like the rounded edges where tabletops meet the sides. This design isn't just about aesthetics; it serves a practical function by eliminating sharp corners that could cause injuries, especially in family homes or busy environments. Additionally, fillets evenly distribute weight and stress, enhancing the structural integrity of the furniture and increasing its durability.
Fillets can be produced through various methods, with machining and 3D printing being the most prevalent. Machining uses mills or lathes to cut a precise, rounded path between surfaces. In 3D printing, the fillet design is integrated into the digital model and formed during the printing process, enabling the creation of intricate fillets with minimal post - processing.
Key Differences
Appearance
The most obvious distinction lies in their shapes. Chamfers feature an angled, flat surface that creates a linear transition between surfaces, imparting a sharp, industrial look. Fillets, in contrast, offer a smooth, curved transition, giving products a softer, more refined appearance. It's important to note that while "bevel" and "chamfer" are sometimes used interchangeably, they are different. A beveled edge extends across the entire length of the plane, whereas a chamfered edge covers only a portion, meaning more material is removed for bevels.
Machining Cost and Complexity
Manufacturing fillets is generally more expensive and time - consuming. Cutting curved radii, especially with milling, requires specific tools for different radii, increasing production complexity. Chamfers, conversely, are quicker and cheaper to produce. Straight - edge cutting, which they require, can often be done with basic tools or even by hand. Adjusting cutting depth or tool paths allows a single tool to create chamfers of various sizes, reducing costs.
Functionality
Safety: Chamfers soften edges but may still leave some sharpness at the transition. Fillets, by completely eliminating sharp corners, offer safer handling.
Stress Distribution: Chamfers can distribute stress to some degree, but sharp corners still form at the intersection with the part's outline, concentrating stress. Fillets distribute stress evenly, reducing the risk of deformation, making them ideal for high - stress areas.
Flow Dynamics: The smooth, curved shape of fillets reduces turbulence and resistance in fluid flow applications. Chamfers, with their flat, angled edges, create a more abrupt transition, potentially causing turbulence and increasing resistance.
When to Choose
Opting for Chamfers
Assembly - Critical Situations: When precise part - to - part fitting is required, chamfers are the go - to. They guide mating components, ensuring seamless connections, such as in chamfered holes for fasteners.
Cost - Conscious Designs: Chamfers are more cost - effective to produce, especially for external surfaces and flat planes, as they can be machined simply and with basic tools.
Industrial Aesthetics: For a modern, industrial look with sharp geometric edges, chamfers enhance the visual design of products, commonly seen in consumer electronics.
Choosing Fillets
High - Load Applications: When parts will bear heavy loads or experience high stress, fillets evenly distribute stress, reducing the risk of cracks and increasing durability.
Performance - Driven Designs: Despite higher manufacturing costs, fillets are preferred when their performance benefits, such as improved fluid flow in pipes, are essential.
Aesthetic Appeal: For a softer, more polished look, fillets enhance the overall appearance of consumer products and industrial designs.
Safety - First Scenarios: In situations where sharp edges pose a risk, fillets' rounded edges reduce the chance of injury, making them common in hand tools and safety - critical equipment.
Corrosion - Prone Environments: Fillets enable uniform coating application, preventing thin or uneven coatings at sharp edges, providing better corrosion resistance.
Conclusion
In conclusion, the choice between chamfers and fillets is a pivotal decision in part design. Chamfers shine in cost - controlled and rapid - production scenarios, while fillets excel in high - stress and performance - oriented applications. Balancing these factors is essential for creating efficient and cost - effective designs.
HL Parts recognizes the significance of this choice. Whether your design calls for chamfers, fillets, or a combination, we are ready to assist. Upload your design for a quick quote and a free Design for Manufacturability (DFM) analysis.