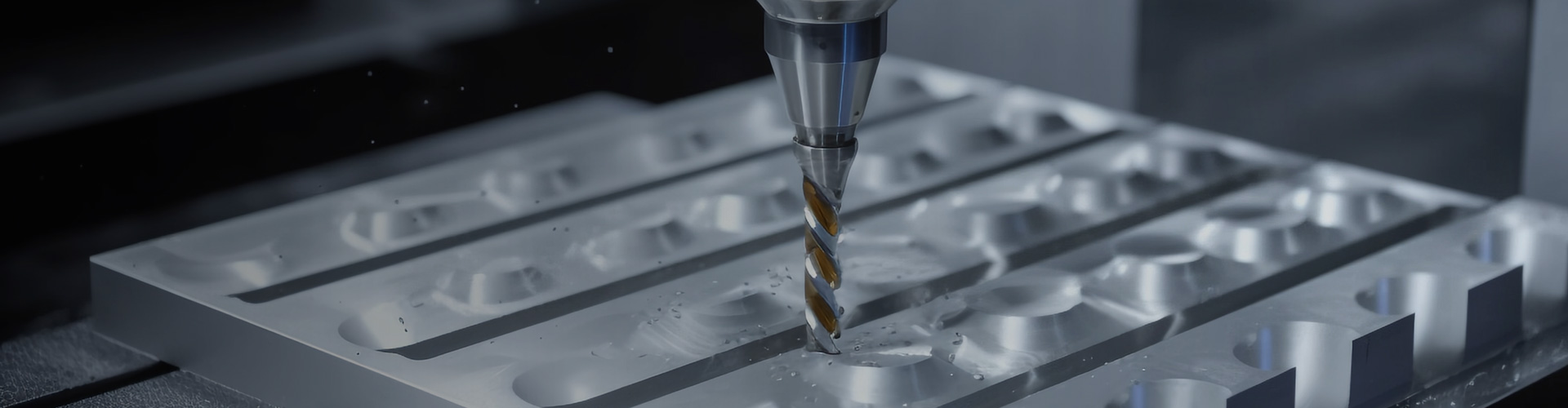
The Differences Between Cast Iron and Steel
Introduction
Both cast iron and steel are ferrous metals mainly composed of iron atoms (Fe on the periodic table). Iron is abundant on Earth but usually exists in an oxidized state. Smelting, a complex and energy - intensive process, is needed to extract elemental iron.
Pure iron, with its strong magnetic properties, is used in making the cores of electromagnetic devices. However, its softness and tendency to deform restrict its use in industrial manufacturing. Thus, it is often alloyed, commonly with carbon, to improve its properties. Cast iron and steel are two widely used metal materials resulting from such improvements. Despite their similar appearance, they have distinct characteristics suitable for different applications. This article will compare them in detail.
What is Cast Iron?
Cast iron is an iron - carbon alloy with a relatively high carbon content, ranging from 2% to 4%. The production process starts with smelting iron ore in a blast furnace to produce pig iron. Then, pig iron is melted together with scrap iron, and the molten metal is poured into molds to solidify, giving cast iron its name.
Besides carbon, it usually contains 1% - 3% silicon, along with small amounts of manganese, phosphorus, and sulfur. Carbon and silicon play key roles in determining its structure and properties. The form and distribution of graphite, which comes from carbon, are crucial in classifying cast iron:
· Gray Cast Iron: Graphite appears as flakes. It has good castability and vibration - damping properties but is brittle.
· White Cast Iron: Carbon exists as iron carbide (Fe3C), making it hard, brittle, and highly wear - resistant.
· Ductile (Nodular) Cast Iron: Graphite is in spherical nodule form, providing high strength and toughness.
· Malleable Cast Iron: Through annealing, carbon is present as clumpy graphite, offering good toughness and machinability.
What is Steel?
Steel is an iron alloy with a carbon content generally less than 2%. It is produced by refining molten pig iron in a basic oxygen furnace (BOF) or electric arc furnace (EAF) to reduce carbon and remove impurities, followed by pouring into molds and cooling.
During production, additional elements are added, and the carbon content is adjusted to create different steel grades with specific properties. For example, while most steel is prone to corrosion, stainless steel, with its low carbon content and at least 10.5% chromium, has excellent corrosion resistance.
Steel can be classified into many types based on composition and use:
· Carbon steel: Mainly alloyed with carbon, further divided into low - carbon, medium - carbon, and high - carbon steel.
· Alloy steel: Contains other alloying elements like chromium, nickel, molybdenum, and vanadium. Stainless steel and tool steel are common alloy steels.
Key Differences
· Carbon Content and Chemical Composition
The most significant difference lies in their carbon content. Cast iron has over 2% carbon, making it harder and more brittle. Steel, with less than 2% carbon, offers more flexibility. Cast iron's silicon content improves its casting properties, while steel often includes alloying elements like chromium, nickel, and molybdenum for enhanced strength, toughness, and corrosion resistance.
· Melting Point
Cast iron melts at 1150°C - 1300°C (2100°F - 2370°F), while steel melts at 1370°C - 1510°C (2500°F - 2800°F). Cast iron's lower melting point gives it better fluidity, facilitating the creation of complex castings. Steel's higher melting point allows it to retain strength during high - temperature processing.
· Castability
Cast iron has excellent castability due to its low melting point and silicon content. It flows well and shrinks less during cooling. Steel, on the other hand, is less fluid, more reactive to molds, and shrinks more, requiring more careful handling during casting.
· Strength
· Tensile Strength: Cast iron has low tensile strength as graphite in its structure acts as stress concentrators. Steel, with a more uniform microstructure, can have high tensile strength through alloying and heat treatment.
· Compressive Strength: Cast iron generally has better compressive strength as its graphite structure disperses stress. Steel has more balanced compressive and tensile strengths.
· Impact Strength: Steel outperforms cast iron in impact resistance due to its ductility. Ductile iron has better impact strength than gray iron but still lags behind steel.
· Wear Resistance
Cast iron resists mechanical wear well because of its hardness and graphite's lubricating effect, but its brittleness limits its use in dynamic environments. Steel, with high toughness, is suitable for dynamic and high - impact applications.
· Corrosion Resistance
Both metals corrode in the presence of oxygen and moisture. However, steel can be alloyed with elements like chromium to improve corrosion resistance, while painting or coating is often used to protect both metals.
· Machinability
Cast iron is easy to machine as graphite lubricates the process and chips break easily. Steel's machinability depends on its composition; hardened or high - carbon steel is difficult to machine, and low - carbon steel can be sticky during machining.
· Weldability
Steel is much more weldable than cast iron. Cast iron's high carbon content and brittleness make it prone to cracking during welding, while steel's low carbon content allows for various welding methods.
· Cost
Cast iron is cheaper as its raw materials are more abundant and its production process is simpler and less energy - intensive compared to steel.
Choosing the Right Metal
Understanding these differences helps in selecting the appropriate metal. Cast iron is ideal for applications requiring good castability, high compressive strength, and wear resistance in static environments. Steel is better for applications that demand high tensile and impact strength, good weldability, and performance in dynamic and corrosive conditions.
Order With HL Parts - One Stop Machining Service
We believe you have now chosen a side in the cast iron vs. steel debate. However, finding the right metal machining services for prototyping and production can still be a challenge.HL Parts is your best choice. Our professional CNC machining and die casting services efficiently handle even difficult-to-machine materials, helping you reduce processing times and save on machining costs.Upload your project to our platform, and you will receive a free quotation and DFM analysis as soon as possible.