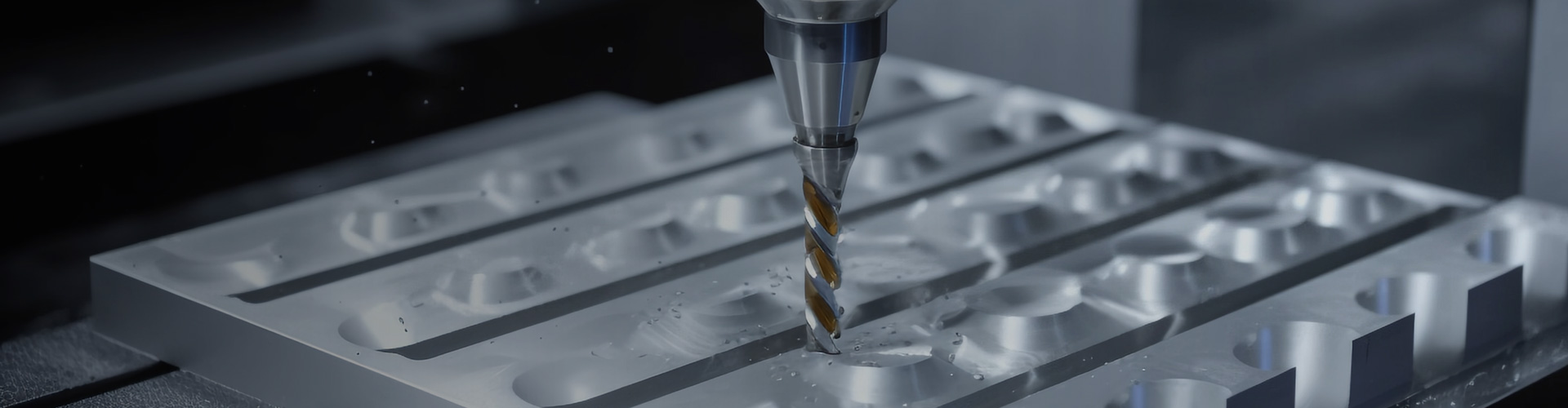
The Types and Selection Criteria of Bearings
Introduction to Bearings: The Unsung Heroes of Machinery
Bearings are fundamental mechanical components that serve as the backbone of virtually all rotating machinery. These precision-engineered devices perform three critical functions: supporting rotating shafts, reducing friction between moving parts, and facilitating smooth motion transmission. By minimizing energy loss through friction reduction, bearings dramatically improve mechanical efficiency and equipment longevity.
From the wheels on your bicycle to the turbines in power plants, bearings enable motion in countless applications. They're present in everyday items like refrigerator hinges and computer hard drives, as well as in industrial equipment such as conveyor systems and wind turbines. This versatility earns bearings the nickname "the joints of machinery" - without them, modern mechanical systems would grind to a halt.
This comprehensive guide will explore bearing anatomy, examine various bearing types, and provide practical advice for selecting the optimal bearing for your specific requirements. Whether you're an engineer specifying components for industrial machinery or a hobbyist working on a personal project, understanding bearings is essential for optimal mechanical design.
Bearing Fundamentals: Anatomy and Terminology
The Structural Components of Bearings
1. Bearing Rings/Races
These hardened steel rings form the foundation of most bearing assemblies:
- In radial bearings, the inner ring mounts directly on the rotating shaft while the outer ring typically remains stationary within the housing
- Thrust bearings utilize shaft races (attached to the rotating component) and housing races (fixed to the stationary structure)
- Precision-ground raceways provide smooth surfaces for rolling elements to traverse
2. Rolling Elements
The load-bearing components that enable smooth motion:
- Available in various geometries including balls, cylindrical rollers, tapered rollers, and needle rollers
- Material selection ranges from standard chrome steel to advanced ceramics for specialized applications
- The shape and size of rolling elements determine the bearing's load capacity and speed capabilities
3. Cage (Retainer)
This crucial component maintains proper spacing between rolling elements:
- Prevents roller-to-roller contact that could cause friction and wear
- Manufactured from steel, brass, or advanced polymers depending on application requirements
- Designs vary from simple stamped steel to complex machined configurations for high-performance applications
4. Auxiliary Components
Additional elements that enhance bearing performance:
- Seals/Shields: Protect internal components from contaminants while retaining lubrication
- Lubrication Systems: Grease fittings or oil circulation ports for continuous lubrication
- Alignment Features: Specialized geometries that compensate for mounting imperfections
Bearing Classification Systems
Bearings can be categorized using several classification methods:
1. By Motion Type
- Rolling Element Bearings: Utilize balls or rollers to minimize friction (e.g., ball bearings, roller bearings)
- Plain Bearings: Rely on sliding surfaces with lubrication (e.g., bushings, sleeve bearings)
2. By Load Direction
- Radial Bearings: Primarily support loads perpendicular to the shaft axis
- Thrust Bearings: Designed for axial loads parallel to the shaft
- Combination Bearings: Engineered to handle both radial and axial loads simultaneously
3. By Rolling Element Shape
- Ball Bearings: Use spherical elements for lower friction at higher speeds
- Roller Bearings: Employ cylindrical, tapered, or spherical rollers for heavier loads
Comprehensive Bearing Types and Their Applications
1. Radial Ball Bearings
Designed primarily for radial loads with contact angles typically under 15°, these versatile bearings come in several configurations:
Deep Groove Ball Bearings
- The workhorse of the bearing world, accounting for over 70% of all bearing applications
- Deep raceways enable support for moderate axial loads in both directions
- Available in sealed, shielded, and open configurations for various environments
- Typical applications: Electric motors, appliances, pumps, and gearboxes
Angular Contact Ball Bearings
- Feature precisely angled raceways (15°-40°) for combined load capability
- Available in single and double row configurations
- Often used in matched pairs (DB, DF, or DT arrangements) for enhanced performance
- Common uses: Machine tool spindles, automotive wheels, and robotics
Self-Aligning Ball Bearings
- Spherical outer ring allows for automatic misalignment compensation (up to 3°)
- Dual-row ball design provides increased radial load capacity
- Ideal for applications with shaft deflection or mounting inaccuracies
- Frequently found in conveyor systems, textile machinery, and agricultural equipment
2. Radial Roller Bearings
Engineered for heavy radial loads, these bearings use various roller geometries to optimize performance:
Cylindrical Roller Bearings
- Linear contact provides superior radial load capacity compared to ball bearings
- Available in single, double, and multi-row configurations
- High-speed capability with proper lubrication and cooling
- Industrial applications: Large electric motors, rolling mills, and wind turbines
Needle Roller Bearings
- Compact design with length-to-diameter ratios exceeding 4:1
- Can operate with or without inner/outer rings for space-constrained applications
- Require hardened and ground raceway surfaces when used without rings
- Common in automotive transmissions, aircraft controls, and medical devices
Tapered Roller Bearings
- Conical geometry enables combined radial and axial load support
- Contact angles typically range from 10°-30° depending on series
- Adjustable clearance through precise mounting practices
- Dominant in wheel bearings, differential systems, and heavy equipment
Spherical Roller Bearings
- Barrel-shaped rollers with spherical outer raceway for self-alignment
- Exceptional shock load and vibration resistance
- Capable of handling significant misalignment (up to 2.5°)
- Heavy industry applications: Mining equipment, paper mills, and marine propulsion
3. Thrust Bearings
Specialized designs for predominantly axial load applications:
Thrust Ball Bearings
- Simple design with 90° contact angle for pure axial loading
- Available in single-direction and double-direction configurations
- Speed limitations due to centrifugal forces on balls
- Typical uses: Automotive clutches, crane hooks, and steering systems
Thrust Roller Bearings
- Various roller types address different application needs:
- Cylindrical thrust rollers: High axial capacity with minimal radial support
- Tapered thrust rollers: Combined load capability with misalignment tolerance
- Spherical thrust rollers: Self-aligning capability for heavy axial loads
- Common in gearboxes, screw presses, and vertical pump applications
4. Specialized Bearing Types
Plain Bearings (Bushings)
- Simplest bearing type with sliding rather than rolling motion
- Require continuous lubrication for proper operation
- Can be made from self-lubricating materials for maintenance-free operation
- Widely used in low-speed, high-load applications like hydraulic cylinders
Fluid Bearings
- Utilize pressurized fluid films to eliminate metal-to-metal contact
- Hydrostatic bearings: Externally pressurized for precision applications
- Hydrodynamic bearings: Generate pressure through shaft rotation
- Common in high-speed spindles, turbines, and precision instruments
Magnetic Bearings
- Contactless operation through electromagnetic levitation
- Require sophisticated control systems but offer frictionless operation
- Used in high-speed applications like turbochargers and flywheel energy storage
Advanced Selection Methodology
Choosing the optimal bearing requires careful consideration of multiple factors:
1. Load Characteristics Analysis
Load Type Identification
- Pure radial loads: Deep groove ball bearings or cylindrical roller bearings
- Pure axial loads: Thrust bearings (ball or roller type)
- Combined loads: Angular contact or tapered roller bearings
Load Magnitude Assessment
- Light-to-moderate loads: Ball bearings typically sufficient
- Heavy loads: Roller bearings preferred for their larger contact areas
- Shock loads: Spherical roller bearings or specially designed alternatives
2. Speed Considerations
Speed Capability Evaluation
- High-speed applications (DN > 1 million): Precision angular contact bearings
- Moderate speeds: Standard deep groove ball bearings
- Low-speed, high-load: Tapered or spherical roller bearings
Lubrication Requirements
- Grease lubrication: Simplified maintenance for moderate speeds
- Oil lubrication: Required for very high speeds or extreme temperatures
- Solid film lubrication: For extreme environments or vacuum applications
3. Precision Requirements
Accuracy Class Selection
- ABEC 1 (ISO Normal): General industrial applications
- ABEC 3/5 (ISO P6/P5): Machine tools and precision equipment
- ABEC 7/9 (ISO P4/P2): Ultra-high precision applications
Runout Specifications
- Radial runout critical for applications like spindle bearings
- Face runout important for thrust bearing applications
- Consider both static and dynamic runout characteristics
4. Environmental Factors
Contamination Protection
- Sealed bearings for dirty or wet environments
- Shielded bearings for cleaner environments requiring less maintenance
- Special coatings for corrosive environments
Temperature Considerations
- Standard bearings: -30°C to +120°C operating range
- High-temperature bearings: Special steels and heat stabilization up to 350°C
- Cryogenic bearings: Special materials for sub-zero applications
Installation and Maintenance Best Practices
Proper Mounting Techniques
1. Interference Fit Guidelines
- Shaft and housing tolerances per ISO standards
- Proper press fit tools to prevent bearing damage
- Thermal installation methods for large bearings
2. Alignment Procedures
- Laser alignment for critical applications
- Dial indicator methods for general precision
- Soft foot correction techniques
Lubrication Management
1. Grease Selection Criteria
- Base oil viscosity matching operating conditions
- Thickener type (lithium, polyurea, clay) for temperature range
- Additive package for special requirements
2. Relubrication Intervals
- Calculated based on bearing type, size, and operating conditions
- Monitoring techniques: Vibration analysis, temperature trending
- Automated lubrication systems for critical applications
Condition Monitoring
1. Vibration Analysis
- Frequency domain analysis for early fault detection
- Envelope detection for bearing fault frequencies
- Trending for predictive maintenance
2. Thermal Monitoring
- Infrared thermography for temperature mapping
- Embedded RTDs for precision temperature measurement
- Thermal modeling for abnormal condition detection
Emerging Bearing Technologies
Smart Bearings
- Integrated sensors for real-time condition monitoring
- Wireless data transmission capabilities
- Predictive maintenance algorithms
Advanced Materials
- Hybrid bearings with ceramic rolling elements
- Self-lubricating composite materials
- Nanostructured coatings for extreme environments
Sustainable Designs
- Extended service life for reduced environmental impact
- Remanufacturing and refurbishment programs
- Eco-friendly lubricant compatibility
Conclusion: Optimizing Bearing Selection for Peak Performance
Selecting the proper bearing requires a systematic approach that considers all operational parameters and environmental conditions. By understanding the complete range of bearing types and their capabilities, engineers can make informed decisions that optimize equipment performance and reliability.
Remember that bearing selection is often iterative - initial choices may need refinement based on actual operating conditions. Consultation with bearing specialists during the design phase can prevent costly mistakes and ensure optimal system performance.
For challenging applications or when in doubt, partnering with bearing experts can provide access to specialized knowledge, custom engineering solutions, and application-specific recommendations that go beyond standard catalog offerings. The right bearing solution not only meets your immediate needs but also contributes to the long-term reliability and efficiency of your mechanical systems