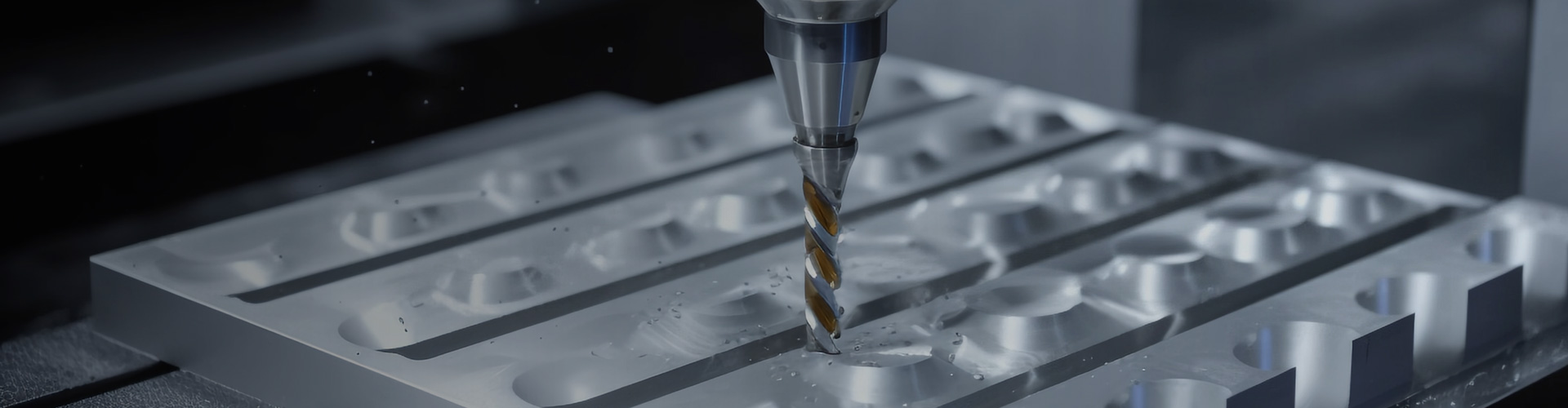
3D Printing: A Comprehensive Guide to Additive Manufacturing Technologies
3D printing, also known as additive manufacturing, has transitioned from a niche prototyping tool in the 1980s to a mainstream production technology capable of manufacturing end-use parts. While initially developed for rapid prototyping, advancements in materials, precision, and speed have expanded its applications to small and medium-scale production.
All additive manufacturing processes begin with a digital CAD model, which is sliced into layers and constructed sequentially by the 3D printer. The technology encompasses multiple methods, each defined by its unique approach to material deposition and fusion. Below, we explore the most common 3D printing processes and their respective technologies.
Material Extrusion: Fused Deposition Modeling (FDM) and Fused Filament Fabrication (FFF)
Material extrusion is one of the most widely recognized 3D printing methods, particularly in consumer-grade machines. In this process, a thermoplastic filament is fed through a heated nozzle, melted, and deposited layer by layer onto a build platform.
- FDM (Fused Deposition Modeling) is the industrial standard, capable of printing durable parts using engineering-grade thermoplastics such as ABS, PC, and PEI. While cost-effective, FDM parts often require post-processing to smooth visible layer lines and remove support structures.
- FFF (Fused Filament Fabrication) is the consumer-friendly counterpart, commonly found in desktop 3D printers. It uses spooled filaments, including PLA, ABS, and flexible TPU, making it ideal for hobbyists and educational use.
Despite its accessibility, material extrusion has limitations in surface finish and dimensional accuracy compared to resin-based or powder-based methods.
Vat Photopolymerization: SLA, DLP, and CLIP
Vat photopolymerization uses liquid resin cured by light to create high-detail parts. This category includes:
- Stereolithography (SLA) – The oldest 3D printing technology, SLA uses a UV laser to cure photopolymer resin layer by layer. It produces smooth, precise parts, making it ideal for dental models, jewelry, and prototypes requiring fine details. However, resin parts are often brittle and require post-curing.
- Digital Light Processing (DLP) – Similar to SLA but uses a digital projector to cure entire layers at once, speeding up print times. DLP is commonly used for dental aligners and intricate prototypes.
- Continuous Liquid Interface Production (CLIP) – Unlike traditional layer-by-layer printing, CLIP grows parts continuously from a resin pool using UV and blue light, enabling faster production and stronger parts.
Resin-based printing excels in detail but requires careful handling due to material toxicity and post-processing needs.
Binder Jetting: Powder-Based Color and Multi-Material Printing
Binder jetting binds powder particles using a liquid adhesive, enabling full-color and multi-material printing. Key variants include:
- Powder Bed and Inkjet Head (PBIH) – An inkjet head deposits binder onto powder layers (ceramics, metals, or sand), creating parts without heat. Excess powder supports complex geometries, but parts may require infiltration for strength.
- Plaster-Based 3D Printing – Uses gypsum powder and binder to produce full-color models, often for architectural or artistic applications. However, parts are fragile and not suitable for functional use.
- ColorJet Printing (CJP) – Similar to PBIH but optimized for vibrant, multi-color models, making it popular for marketing prototypes and figurines.
Binder jetting is fast and cost-effective but lacks the strength of sintered or melted powder methods.
Powder Bed Fusion: High-Strength Metal and Plastic Parts
Powder bed fusion (PBF) uses lasers or electron beams to fuse powdered materials, producing durable functional parts. Major PBF technologies include:
- Selective Laser Sintering (SLS) – A laser sinters nylon or thermoplastic powders, creating robust parts without supports. Ideal for aerospace and automotive components.
- Direct Metal Laser Sintering (DMLS) & Selective Laser Melting (SLM) – These metal 3D printing methods fuse metal powders (aluminum, titanium, steel) for high-performance industrial parts. SLM fully melts the powder, while DMLS sinters it, affecting part density.
- Electron Beam Melting (EBM) – Uses an electron beam in a vacuum to melt metal powders, reducing residual stress for aerospace and medical implants.
- Selective Heat Sintering (SHS) – A lower-cost alternative to SLS, using a thermal print head instead of a laser.
PBF excels in strength and complexity but requires extensive post-processing and has high material costs.
Direct Energy Deposition: Large-Scale Metal Printing
This method deposits and fuses material simultaneously using a laser or electron beam:
- Laser Metal Deposition (LMD) – Blows metal powder into a laser-generated melt pool, ideal for repairing turbine blades or creating large metal structures.
- Electron Beam Additive Manufacturing (EBAM) – Uses an electron beam to melt metal wire, enabling rapid production of large aerospace components.
DED is best for industrial repairs and large parts but lacks fine detail.
Material Jetting: High-Precision Multi-Material Printing
Similar to inkjet printing, material jetting deposits droplets of photopolymer resin, cured by UV light:
- Multi-Jet Fusion (MJF) – Uses fusing agents to create strong nylon parts with fine details.
- PolyJet – Jets multiple materials simultaneously, allowing flexible, rigid, and colored sections in a single print.
Material jetting offers unmatched precision but is expensive and limited to photopolymers.
Sheet Lamination: Low-Cost Layered Manufacturing
Sheets of material (paper, plastic, or metal) are bonded and cut into shape:
- Laminated Object Manufacturing (LOM) – Glues and laser-cuts layers for rapid prototyping.
- Ultrasonic Consolidation (UC) – Bonds metal foils using ultrasonic welding, useful for lightweight aerospace structures.
Sheet lamination is fast and affordable but lacks the precision of other methods.
The Future of 3D Printing
As additive manufacturing advances, it continues to bridge the gap between prototyping and full-scale production. Innovations in speed, material diversity, and post-processing are driving adoption across industries, from healthcare to aerospace. Whether for prototyping, custom manufacturing, or industrial applications, 3D printing offers unparalleled flexibility in modern manufacturing.
For specialized materials and manufacturing solutions, platforms like Xometry provide access to a wide range of 3D printing technologies tailored to production needs.
Order 3D Printed Parts with Advanced Finishing Options
3D printing has revolutionized manufacturing by offering rapid prototyping and production capabilities for complex, custom-designed parts. With a variety of materials and post-processing finishes available, 3D-printed components can achieve enhanced durability, aesthetics, and functional performance.
Whether you need high-strength metal parts, smooth resin prototypes, or flexible thermoplastic components, 3D printing provides versatile solutions across industries such as aerospace, automotive, medical, and consumer products. Advanced post-processing techniques—such as sanding, polishing, dyeing, and sealing—can further refine surface quality and mechanical properties.
If you're unsure which 3D printing technology or material best suits your project, contact HL Parts today to discuss your requirements. Our experts can guide you through material selection, finishing options, and design optimizations to ensure optimal performance for your application.
For more details on available materials and surface finishes or request a quote to get started on your next 3D printing project.