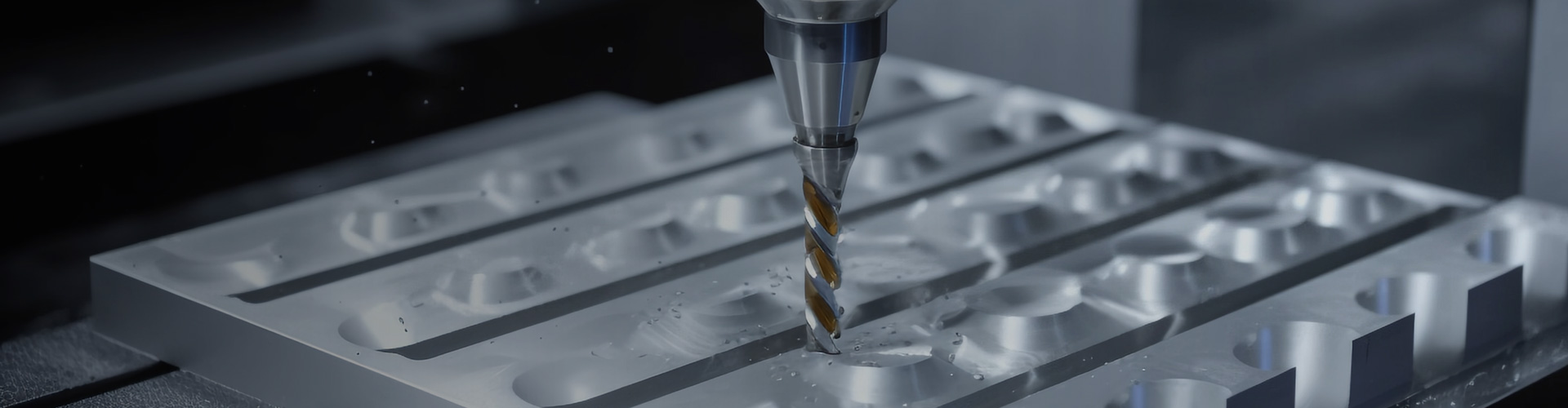
Detailed Guides and Charts of Metal Strength
Metal strength is one of the most essential mechanical properties in determining a metal's suitability for given applications. It signifies how well a metal can resist external loads or force without deforming or breaking. Metals with high strength are invaluable in construction, machinery, and aerospace, where they support structures and withstand extreme conditions.
In this guide, we will distinguish the types of strength, discuss the factors that influence metal strength and how they can be manipulated to enhance a metal's performance. Additionally, we will provide a metal strength chart to help you choose the metal material you want more intuitively.
Types of Metal Strengths
Tensile Loading: Forces that pull or stretch the material.
Compressive Loading: Forces that push or compress the material.
Shear Loading: Forces that act parallel to the surface of a material, causing the material to experience layers or planes sliding past each other.
Bending (Flexural) Loading: Forces that cause the material to bend.
Torsional Loading: Forces that twist the material.
Impact Loading: Sudden, forceful impact or shock loads.
Next, we will discuss in detail several of the most common types of strength.
1. Tensile Strength
Tensile strength defines the maximum tensile (stretching or pulling) stress a material can endure before fracturing. It quantifies a material's load-bearing capacity under tension and is a key indicator of its mechanical reliability.
The stress-strain curve illustrates a material's behavior under tensile forces, with three critical points (A, B, and C) marking key transitions in its response. Below, we examine each of these points in detail:
Yield Strength (Point A)
The yield strength marks the stress threshold beyond which a material undergoes permanent deformation. Once exceeded, the material will not return to its original shape, even after the load is removed. Engineers rely on this value to establish safe operational limits, ensuring structures and components maintain integrity under expected loads. Many industry standards use yield strength as a benchmark for material failure.
Ultimate Tensile Strength (Point B – UTS)
Often referred to simply as "tensile strength," the Ultimate Tensile Strength (UTS) represents the peak stress a material can sustain before necking begins. Beyond this point, localized thinning occurs, reducing the cross-sectional area and leading to eventual fracture.
How Tensile Strength is Measured
A tensile testing machine (or Universal Testing Machine, UTM) is used to evaluate a metal's tensile properties. The machine secures a specimen between two grips and applies a controlled pulling force until failure. Throughout the test, stress and elongation data are recorded, allowing engineers to determine both yield and ultimate tensile strength.
This analysis helps in selecting the right material for applications where strength and durability are critical.
2. Compressive Strength
Compressive strength quantifies a material's ability to withstand forces that push or squeeze it, measuring the maximum load it can sustain before buckling or fracturing. This property is particularly crucial in applications where materials face crushing pressures, such as structural supports, foundations, and heavy machinery components.
How Compressive Strength is Tested
A compression testing machine applies controlled pressure to a specimen using parallel plates that exert force from opposite directions. The test continues until the material begins to deform or fails completely. The stress level at which permanent deformation occurs defines the material's compressive strength.
Understanding this property helps engineers select materials capable of enduring high-pressure environments while maintaining structural stability.
3. Impact Strength
Impact strength evaluates how well a material can absorb sudden shocks or blows without cracking or breaking. This property indicates the material's toughness—its ability to withstand high-energy impacts in real-world applications, from construction to automotive components.
Measuring Impact Resistance
Specialized impact testing machines, like Charpy or Izod testers, determine this property by striking a notched sample with a weighted pendulum. The amount of energy the specimen absorbs before fracturing provides a quantitative measure of its impact strength.
This characteristic is vital for materials used in environments where unexpected stress or collisions may occur, ensuring durability and safety under dynamic loading conditions.
Why do We Need to Learn About Metal Strength?
The Critical Role of Metal Strength in Engineering Applications
Metal strength serves as a fundamental parameter that directly influences material selection and engineering outcomes across industries. Its proper understanding enables professionals to balance performance requirements with practical constraints.
Ensuring Structural Integrity and Longevity
The appropriate metal strength selection forms the foundation for safe and durable structures in critical applications like heavy machinery, architectural frameworks, and transportation infrastructure. Precise strength matching prevents catastrophic failures while maximizing service life, significantly lowering maintenance demands and replacement cycles.
Performance Enhancement Through Material Science
Strategic application of metal strength principles drives efficiency improvements in weight-sensitive sectors. Aerospace and automotive engineers leverage high-strength alloys to achieve optimal strength-to-weight ratios, resulting in enhanced fuel economy, payload capacity, and operational performance.
Economic Optimization in Manufacturing
Informed metal strength selection creates substantial cost advantages throughout product lifecycles. Proper material matching reduces waste during fabrication, minimizes premature failures in service, and optimizes total ownership costs - from initial production through decades of operation.
Enabling Advanced Engineering Solutions
Contemporary material strength understanding facilitates breakthrough innovations across engineering disciplines. This knowledge empowers designers to develop revolutionary structures with unprecedented combinations of lightness, durability, and functionality - continually expanding the horizons of technical achievement.
This comprehensive approach to metal strength analysis transforms theoretical material properties into practical engineering advantages across all phases of design, production, and operation.
Strongest Metals Used in Metal Fabrication
High-Strength Metals and Their Industrial Applications
The following metals and alloys are widely utilized across industries due to their exceptional strength characteristics and performance advantages:
1. Titanium – The Lightweight Powerhouse
- Key Properties: Outstanding strength-to-weight ratio combined with superior corrosion resistance
- Common Alloy: Ti-6Al-4V (titanium-aluminum-vanadium)
- Primary Applications:
- Aerospace components
- Medical implants and surgical tools
- High-performance automotive parts
- Marine hardware
2. Tungsten – The Extreme-Performance Metal
- Key Properties:
- Highest tensile strength among natural metals (up to 1,725 MPa)
- Exceptional heat resistance (highest melting point)
- Common Form: Tungsten carbide (WC) for enhanced toughness
- Primary Applications:
- Cutting tools and drill bits
- Armor-piercing ammunition
- High-temperature furnace components
- Wear-resistant industrial surfaces
3. Chromium – The Hardening Agent
- Key Properties:
- Extreme hardness (8.5 Mohs)
- Excellent corrosion resistance
- Common Uses:
- Protective plating for metals/plastics
- Critical alloying element in stainless steel
- Wear-resistant surface coatings
4. Steel Variants – The Engineering Backbone
A. Stainless Steel
- Composition: Iron-chromium (+ manganese/nickel)
- Strength: 1,560 MPa yield, 1,600 MPa ultimate tensile
- Applications: Medical devices, food processing, architectural structures
B. HSLA Steel
- Features: Microalloyed with vanadium/niobium
- Advantages: High strength with reduced weight
- Uses: Automotive frames, bridges, pressure vessels
C. Maraging Steel
- Characteristics: Ultra-high strength through aging treatment
- Specialty Uses: Rocket components, aircraft landing gear
D. Tool Steel
- Key Attributes: Exceptional hardness and thermal stability
- Industrial Role: Cutting dies, mold tools, machining bits
E. Inconel® Superalloys
- Performance: Maintains strength at extreme temperatures
- Critical Applications: Jet engines, chemical reactors
These materials represent the pinnacle of metallic strength, each offering unique advantages for demanding engineering applications where performance and reliability are paramount. Their continued development pushes the boundaries of what's possible in modern manufacturing and construction.
How to Improve the Strength of Metal?
Advanced Methods for Enhancing Metal Strength
While alloying remains fundamental for improving metal properties, modern fabrication employs several sophisticated techniques to push material performance beyond conventional limits. These methods manipulate the metal's microstructure to achieve superior mechanical characteristics.
1. Solid Solution Strengthening
- Mechanism: Introduces alloying atoms into the host metal's crystal lattice
- Effect: Creates atomic-scale distortions that obstruct dislocation movement
- Outcome: Significant increase in yield strength while maintaining base metal characteristics
2. Precision Heat Treatment Techniques
A. Quenching & Tempering Duo
- Process:
- Quenching: Rapid cooling from austenitizing temperature forms hard martensite
- Tempering: Moderate reheating relieves stresses and optimizes toughness
- Benefits: Achieves optimal balance between hardness and impact resistance
B. Normalizing
- Method: Controlled heating followed by air cooling
- Advantage: Produces uniform, refined grain structure for consistent strength
C. Precipitation Hardening
- Technique: Controlled aging at intermediate temperatures
- Result: Nanoscale precipitates that dramatically increase yield strength
- Applications: Critical for aerospace alloys and high-performance materials
3. Cold Working (Strain Hardening)
- Process: Mechanical deformation at ambient temperature
- Methods Include:
- Cold rolling
- Wire drawing
- Hydroforming
- Strengthening Mechanism: Increased dislocation density creates barriers to further deformation
- Additional Benefit: Improves surface finish and dimensional accuracy
These advanced processing techniques enable engineers to tailor material properties with exceptional precision, meeting the rigorous demands of cutting-edge applications in aerospace, automotive, and energy sectors. The strategic combination of these methods often yields materials with unprecedented performance characteristics.
Metal Strength Chart
The metal strength chart provides a reliable criterion for choosing well-suited materials for specific applications. It provides a comprehensive evaluation of a metal's performance under various loading conditions. You can use it to compare the properties of different metals quickly.
Work with HL Parts for Metal Selection and Machining
Still struggling with choosing the ideal metals for your projects? Don’t worry. HL Parts is your trusted partner! We’re ready here to guide you through the complexities of metal selection and machining. With over a decade of industry experience, we possess the insight and know-how to tackle challenging material requirements.
Strength vs Ductility vs Toughness
Key Material Properties Explained Through Stress-Strain Analysis
Understanding a material's mechanical behavior requires careful differentiation between several critical properties, all visible on the stress-strain curve:
Strength Characteristics
1. Ultimate Tensile Strength (UTS)
- The peak stress value reached before necking begins
- Represents maximum load-bearing capacity
2. Yield Strength
- The stress threshold where elastic deformation transitions to permanent plastic deformation
- Crucial for determining safe working loads
Deformation Capacity
3. Ductility
- Quantified by percent elongation before fracture
- Indicates formability and crashworthiness
4. Resilience
- Energy absorbed during elastic deformation (triangular area under elastic region)
- Important for spring applications
Energy Absorption
5. Toughness
- Total energy absorption until fracture (total area under curve)
- Requires optimal strength-ductility combination
- Brittle materials typically show poor toughness
Surface Properties
6. Hardness
- Resistance to surface indentation and abrasion
- Generally correlates with strength but depends on microstructure
- Measured separately via Rockwell/Brinell/Vickers tests
These interrelated properties form the foundation for material selection in engineering design. The stress-strain curve serves as a powerful visualization tool, revealing how a material responds to loading throughout all deformation stages - from initial elasticity through plastic flow to ultimate failure. Proper interpretation enables engineers to match material capabilities with application requirements.