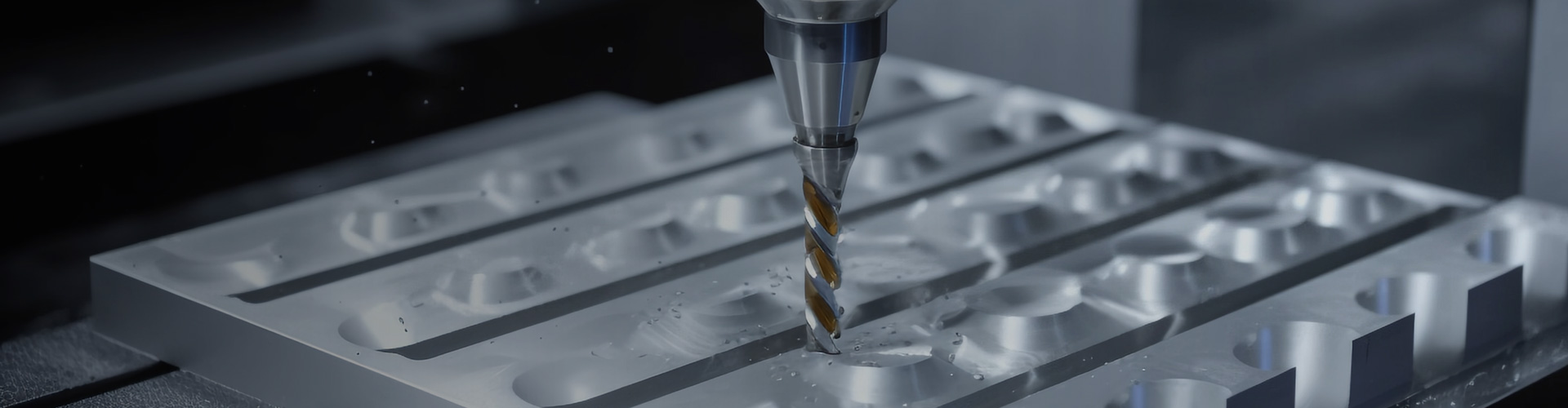
3D Printing and CNC Machining for Your Project
3D printing and CNC machining stand as two leading manufacturing technologies in modern industry. Both utilize digital control systems to facilitate rapid prototyping and excel at producing precision custom components for final applications.
Despite their shared capabilities, these processes diverge fundamentally—often competing directly in the production of solid parts. Their core distinction lies in their approach: one constructs components additively, layer upon layer, while the other achieves shapes subtractively by cutting away material. If you're weighing the choice between CNC machining and 3D printing for your project, understanding their differences is key.
What Is 3D Printing?
3D printing, or additive manufacturing, constructs three-dimensional objects from digital models by depositing material layer by layer. The process starts with a digital design, which can be created using CAD software, captured via 3D scanning, or sourced from online libraries. This model is then processed by slicing software, which divides it into thin horizontal layers and generates machine-readable instructions (typically G-code). If the design includes overhangs or complex geometries, the software may automatically add temporary support structures to ensure print stability. The 3D printer then follows these instructions, precisely depositing and fusing material one layer at a time until the final part is complete.
Evolution of 3D Printing Technologies
The first commercial 3D printing systems emerged in the late 1980s with Chuck Hull’s invention of stereolithography (SLA). Since then, advancements in materials and techniques have led to a variety of 3D printing methods, each suited for different applications:
- FDM (Fused Deposition Modeling):
- Extrudes heated thermoplastic filament through a nozzle, building parts layer by layer.
- Advantages: Low cost, user-friendly, and capable of large-scale prints.
- Limitations: Struggles with overhangs and fine details; parts may show layer lines and have weaker Z-axis strength.
- SLA (Stereolithography):
- Uses UV lasers to cure liquid resin into solid layers.
- Produces smooth, high-detail surfaces, making it ideal for dental models, jewelry, and precision prototypes.
- DLP (Digital Light Processing):
- Similar to SLA but uses a digital projector to cure entire resin layers at once, increasing speed.
- Offers sharp details but may exhibit pixelation and typically has a smaller build volume.
- SLS (Selective Laser Sintering):
- Fuses powdered materials (like nylon) with a laser, using unsintered powder as natural support.
- Enables complex, interlocking geometries with good mechanical strength but a slightly rough surface finish.
- DMLS (Direct Metal Laser Sintering):
- A metal-specific variant of SLS that partially melts powder particles, producing strong but slightly porous parts.
- Requires support structures to prevent warping and often needs post-processing for full density.
- SLM (Selective Laser Melting):
- Fully melts metal powder, creating dense, high-strength components comparable to traditionally cast or forged parts.
- Best suited for pure metals and certain alloys but generates significant thermal stress, necessitating robust supports.
Each of these technologies offers unique advantages, making 3D printing a versatile solution for prototyping, functional parts, and customized manufacturing.
What Is CNC Machining?
CNC (Computer Numerical Control) machining is a well-established subtractive manufacturing process that transforms raw material into finished parts by removing excess material with high precision. Originating from early Numerical Control (NC) systems in the 1950s, CNC machining has advanced with digital automation, becoming a cornerstone of modern manufacturing across industries.
How CNC Machining Works
1. Design & Programming: A part is first modeled in CAD (Computer-Aided Design) software, then converted into machine instructions (G-code) using CAM (Computer-Aided Manufacturing) software.
2. Workpiece Setup: The raw material (metal, plastic, or composite) is securely clamped onto the CNC machine.
3. Tool Selection & Machining: The CNC machine follows the programmed G-code, using specialized cutting tools to shape the workpiece—first with rough machining to remove bulk material, then fine machining for precise dimensions and surface finish.
Common CNC Machining Processes
- CNC Milling:
- Employs rotating multi-point cutting tools to carve out flat surfaces, slots, holes, and complex 3D contours.
- Ideal for producing engine blocks, molds, and structural components in aerospace, automotive, and electronics industries.
- CNC Turning:
- Uses a stationary cutting tool against a rotating workpiece to create cylindrical or conical shapes.
- Perfect for manufacturing shafts, bolts, and hydraulic fittings with tight tolerances.
- Wire EDM (Electrical Discharge Machining):
- Cuts conductive materials using a thin, electrically charged wire, allowing for intricate shapes without mechanical force.
- Commonly used for tool & die making, aerospace components, and medical implants requiring extreme precision.
- Die Casting (Complementary Process):
- While not a CNC process, die casting is another key manufacturing method where molten metal is injected into a steel mold under high pressure.
- Produces high-volume metal parts with excellent dimensional accuracy, such as automotive housings, consumer electronics, and industrial components.
CNC machining remains a dominant force in precision manufacturing, offering unmatched accuracy and repeatability for both prototyping and large-scale production. When combined with processes like die casting, it enables a wide range of high-performance industrial applications.
When to Choose 3D Printing vs. CNC Machining
Each technology brings distinct strengths to manufacturing—CNC machining excels in precision and material flexibility, whereas 3D printing shines when producing intricate designs and accelerating prototyping. The optimal selection hinges on multiple considerations such as material needs, part complexity, turnaround time, and cost factors.
Quick reference table
The quick check table below provides a brief comparison to help you determine which process best suits your needs, or if a combination of both might produce optimal results.
Factors | 3D Printing | CNC Machining |
Material Selection | ▪ Limited but expending options | ▪ Wide range , including metals, plastics, wood, and composites |
Design Complexity | ▪ Can achieve highly complex geometries, including lattice structures and organic shapes | ▪ Can produce parts with relatively complex features, such as threaded holes, sharp edges, and curves |
Precision | ▪ Moderate precision, typically ±0.1 mm, though high-end printers can achieve tighter tolerances | ▪ High precision, often ±0.005 mm or better, depending on material and machine |
Surface Finish | ▪ Requires post-processing (e.g. sanding, painting) for a smooth finish | ▪ Smooth finish with little to no post-processing (typical 125 Ra finish as machined) |
Large Part Size | ▪ Up to 914 x 610 x 914 mm (e.g. FDM) | ▪ Up to 2000 x 800 x1000 mm |
Strength | ▪ In FDM, layer adhesion and print orientation reduce the strength of parts | ▪ The internal structure of parts is continuous, and their strength usually remains at 100% of the native material |
Setup | ▪ Minimal setup, require only a digital file and slicer software | ▪ Need workpiece fixation, tool selection, and machine calibration |
Speed of build | ▪ Low setup time, but build time can take hours | ▪ Can take ages to set up and program, but cutting can be very fast |
Cost | ▪ Cost-effective for small series or custom one-offs | ▪ More economical for high-volume production |
3D Printing vs. CNC Machining: What material do you plan to use?
Both 3D printing and CNC machining are compatible with metals and plastics, though their material capabilities differ significantly. CNC machining demonstrates superior material versatility, predominantly employed for metal parts while increasingly accommodating plastics. Beyond these, CNC technology can also process wood, composite materials, foams, and even wax with precision.
Key CNC materials include:
• Metals: Aluminum alloys, Stainless steels, Titanium grades, Brass
• Engineering Plastics: ABS, Nylon (PA), Polycarbonate, High-performance PEEK
3D printing primarily utilizes thermoplastics, photopolymer resins, and select metal powders. While metal 3D printing exists, it traditionally carries higher costs - though this economic barrier is gradually diminishing.
Common 3D printing materials encompass:
• Polymers: Nylon (PA), PLA, ABS, ULTEM (PEI), ASA, Flexible TPU
• Metal Powders: Aluminum alloys, Stainless steels, Titanium alloys, Inconel superalloys
An important consideration involves material limitations: Highly elastic materials like TPU and silicone often prove challenging for CNC machining due to deformation under cutting forces. Conversely, certain superalloys present machining difficulties because of their extreme strength, tendency for work hardening, and thermal resistance. In these specific cases, 3D printing frequently emerges as the more viable manufacturing solution.
3D Printing vs. CNC Machining: Which is better for complex parts?
While advanced 5-axis CNC machines can produce intricate geometries, they still face inherent limitations when manufacturing parts with internal cavities or complex undercuts due to tool accessibility constraints. The physical dimensions of cutting tools also prevent the creation of perfectly sharp internal corners. Furthermore, specialized fixtures are frequently required to secure workpieces, adding complexity and cost to the machining process.
3D printing overcomes these geometric restrictions by its very nature. The additive process effortlessly creates sophisticated designs with internal channels, organic shapes, and complex features that would be unmanufacturable through subtractive methods. Although some 3D printing technologies require support structures (particularly in metal SLM processes), this post-processing requirement doesn't compromise the technology's unparalleled capacity for producing geometrically complex components with design freedom unmatched by conventional machining.
Does 3D printing or CNC machining offer better dimensional accuracy?
When comparing dimensional accuracy, CNC machining maintains a clear advantage over 3D printing. The subtractive nature of CNC allows for exceptionally tight tolerances, routinely achieving precision within ±0.025mm (0.001") or finer. Meanwhile, even the most accurate 3D printing methods like SLA typically reach about ±0.1mm tolerance under optimal conditions, constrained by inherent factors like material curing shrinkage and nozzle/laser resolution limits.
The consistency gap becomes even more apparent in production runs. CNC's mechanical stability, controlled cutting parameters, and predictable material removal deliver unmatched repeatability. 3D printing, while revolutionary for complex geometries, faces consistency challenges from variables including thermal-induced warping, interlayer bonding variations, and sensitivity to ambient conditions like temperature and humidity. These fundamental process differences make CNC the undisputed choice when micrometer-level precision and batch-to-batch uniformity are critical requirements.
How does the surface finish compare between 3D printing and CNC machining?
When it comes to surface quality, both manufacturing methods offer distinct advantages with opportunities for enhancement. While high-resolution 3D printers such as SLA systems can achieve impressively smooth finishes with detailed surface textures, CNC machining often surpasses these results when equipped with precision finishing tools.
The true potential of both technologies emerges through post-processing treatments. CNC-produced components benefit from professional finishing techniques including:
- Protective anodization
- Durable powder coating
- Uniform bead blasting
- Corrosion-resistant passivation
Similarly, 3D printed parts can be elevated through various finishing processes:
- Metal plating for enhanced conductivity
- Surface polishing for optical clarity
- Bead blasting for uniform texture
- Thermal treatments to improve material properties
These finishing options allow both CNC and 3D printed components to meet demanding aesthetic requirements while improving functional performance, demonstrating that surface quality ultimately depends more on post-processing than the core manufacturing method itself.
How many parts are you manufacturing and is cost a primary concern?
When selecting a manufacturing method for standard geometry parts, the optimal choice depends primarily on material type and production volume.
For polymer components:
• Prototype/low-volume (1-10 pieces): 3D printing offers the fastest turnaround with minimal setup
• Small batches (10-100 pieces): Both 3D printing and CNC machining become viable options
• Medium runs (100-1000 pieces): CNC machining gains cost advantage through distributed setup costs, with injection molding entering consideration
• Mass production (1000+ pieces): Injection molding becomes the most economical solution
For metallic components, the production economics differ significantly:
• Prototype to medium runs (1-100 pieces): CNC machining typically provides better value than metal AM
• Production quantities (100-1000 pieces): CNC remains standard, though investment casting may compete
• High-volume needs (1000+ pieces): Casting processes (investment or die casting) offer superior cost efficiency
The crossover points between these technologies vary based on part complexity, material specifications, and required tolerances, with each method having its ideal application window in the production volume spectrum.
HL Parts’s Top Tips for Choosing Between 3D Printing & CNC Machining
lecting the right manufacturing technology for your custom parts may seem like an insurmountable challenge, but it doesn’t have to be. As we always tell our customers at HL Parts, there is no perfect, one-size-fits-all manufacturing method. The best choice depends on a variety of factors. To help guide your decision, we've put together a few essential rules of thumb:
Choose CNC machining if you're producing parts in medium to high quantities with relatively simple geometries.
Choose CNC machining if precision and durability are key, especially for applications requiring long-term reliability, such as aerospace and medical components.
Choose 3D printing for lower quantities of parts or rapid prototypes, particularly if your designs have complex geometries.
When dealing with metal parts, CNC machining can be price-competitive even for low quantities, but geometry limitations still apply.
Still unsure which manufacturing method is right for your project? Our expert engineering team is ready to help! Simply upload your design files and let HL Parts - China's premier CNC machining and 3D printing service provider - analyze your requirements and recommend the optimal solution. With decades of combined experience, we'll guide you to the perfect manufacturing approach for your specific needs. Get started today!